Boosting Flow Control Efficiency with Pneumatic Ball Valves
In today's demanding industrial landscape, achieving optimal flow control efficiency is paramount for operational success across petrochemical, power generation, and manufacturing sectors. Pneumatic Ball Valves have emerged as the cornerstone solution for enterprises seeking superior performance, reliability, and cost-effectiveness in their fluid control systems. These advanced valves combine the proven reliability of ball valve technology with the precision and speed of pneumatic actuation, delivering unmatched control capabilities that directly translate to enhanced productivity, reduced operational costs, and improved system safety. With their ability to provide rapid response times, precise flow modulation, and exceptional durability even in the most challenging operating conditions, pneumatic ball valves represent the optimal choice for modern industrial applications demanding both efficiency and reliability.
Key Advantages of Pneumatic Ball Valves in Industrial Applications
Enhanced Response Speed and Control Precision
Pneumatic Ball Valve technology delivers exceptional response times that significantly outperform traditional manual and electric valve systems. The compressed air actuation mechanism enables valve operation speeds of less than one second for full stroke completion, making these valves ideal for applications requiring rapid flow adjustments or emergency shutdown scenarios. This lightning-fast response capability is particularly crucial in petrochemical processing where instantaneous flow control can prevent equipment damage, reduce product waste, and enhance overall system safety. The precision control offered by pneumatic actuation systems allows for accurate positioning within ±0.1% of the desired valve position, ensuring consistent flow rates and optimal process control. Modern pneumatic ball valves incorporate advanced positioner technology that maintains precise valve positioning even under varying process conditions, eliminating the drift and hunting commonly associated with less sophisticated control systems. This level of precision translates directly to improved product quality, reduced energy consumption, and enhanced operational efficiency across diverse industrial applications.
Superior Durability and Maintenance Efficiency
The robust construction of Pneumatic Ball Valve assemblies ensures exceptional longevity and minimal maintenance requirements, making them highly cost-effective over their operational lifespan. These valves feature hardened stainless steel or specialized alloy ball and seat components that resist wear, corrosion, and erosion even when handling abrasive or chemically aggressive media. The pneumatic actuation system eliminates the mechanical wear points common in manual valve operations, significantly extending service intervals and reducing maintenance costs. Advanced sealing technologies, including PTFE and specialized elastomer seat materials, provide reliable shutoff performance for thousands of operating cycles while maintaining zero leakage ratings. The self-cleaning action of the rotating ball element prevents buildup of deposits and contaminants that could compromise valve performance, further extending maintenance intervals. Many pneumatic ball valves incorporate diagnostic capabilities that monitor actuator air pressure, valve position, and operating cycles, enabling predictive maintenance strategies that prevent unexpected failures and optimize maintenance scheduling.
Versatile Application Range and System Integration
Pneumatic Ball Valve systems demonstrate remarkable versatility across pressure ranges from vacuum service to 6000 PSI and temperature ranges from cryogenic applications to 500°C, accommodating virtually any industrial process requirement. These valves excel in handling diverse media including corrosive chemicals, high-viscosity fluids, slurries, and gases while maintaining consistent performance characteristics. The modular design of pneumatic actuators allows for easy integration with existing control systems, supporting both analog and digital control signals including 4-20mA, 0-10V, and various fieldbus protocols. Advanced pneumatic ball valves incorporate fail-safe mechanisms that automatically position the valve to a predetermined safe position upon air supply failure, ensuring process safety and equipment protection. The compact actuator design minimizes installation space requirements while providing high torque output capabilities, making these valves suitable for applications where space constraints would prohibit larger electric actuators. Integration with modern process control systems enables remote operation, automated sequencing, and real-time performance monitoring that enhances overall system efficiency and operational visibility.
Optimizing System Performance Through Advanced Pneumatic Ball Valve Technology
Smart Positioning and Feedback Systems
Modern Pneumatic Ball Valve assemblies incorporate sophisticated digital positioner technology that revolutionizes flow control accuracy and system responsiveness. These intelligent positioning systems utilize advanced algorithms to compensate for process variables such as pressure fluctuations, temperature changes, and flow turbulence, maintaining precise valve positioning regardless of operating conditions. Digital positioners provide comprehensive diagnostic feedback including valve position confirmation, actuator health monitoring, and performance trend analysis that enables proactive maintenance strategies and optimal system performance. The integration of smart positioner technology allows for valve characterization and linearization, ensuring that control signals correspond directly to desired flow rates across the entire operating range. Advanced pneumatic ball valves feature dual-acting actuators with integral position feedback that provides precise control in both opening and closing directions, eliminating overshooting and oscillation that can compromise process stability. The diagnostic capabilities of modern positioners include air consumption monitoring, stroke time analysis, and signature verification that identifies potential issues before they impact system performance.
Energy Efficiency and Environmental Considerations
Pneumatic Ball Valve systems offer significant energy advantages compared to electric actuated alternatives, particularly in applications requiring high-speed operation or frequent cycling. The inherent efficiency of pneumatic actuation systems, combined with modern air preparation and distribution technologies, results in lower overall energy consumption and reduced environmental impact. Advanced pneumatic ball valves incorporate low-friction bearing systems and optimized flow passages that minimize pressure drop and reduce pumping energy requirements throughout the system. The fail-safe design characteristics of pneumatic actuation provide inherent safety advantages that reduce the risk of environmental releases or process upsets, supporting corporate sustainability initiatives and regulatory compliance. Modern pneumatic systems utilize precise air consumption control and exhaust recovery technologies that minimize compressed air waste and reduce overall utility costs. The rapid cycling capability of pneumatic ball valves enables more responsive process control that optimizes energy usage by maintaining processes closer to ideal operating conditions, reducing energy waste associated with process variations and overshooting.
Integration with Industry 4.0 and Digital Transformation
The evolution of Pneumatic Ball Valve technology embraces Industry 4.0 principles through advanced connectivity and data analytics capabilities that transform traditional valve operations into intelligent system components. Modern pneumatic ball valves support various digital communication protocols including HART, Foundation Fieldbus, and Profibus that enable seamless integration with distributed control systems and plant asset management platforms. Advanced diagnostic capabilities provide real-time performance data that supports predictive maintenance strategies, reducing unplanned downtime and optimizing maintenance resource allocation. The integration of artificial intelligence and machine learning algorithms with pneumatic ball valve systems enables automated optimization of control parameters based on historical performance data and process conditions. Smart pneumatic ball valves incorporate edge computing capabilities that process local data and provide immediate response to changing conditions while communicating relevant information to higher-level control systems. The digital transformation of pneumatic valve technology enables remote monitoring and control capabilities that support centralized operations and reduce the need for on-site intervention, improving both operational efficiency and worker safety.
Selection Criteria and Implementation Best Practices
Application-Specific Design Considerations
Selecting the optimal Pneumatic Ball Valve configuration requires comprehensive analysis of specific application requirements including flow characteristics, pressure and temperature conditions, media properties, and control performance expectations. Critical sizing parameters include Cv coefficient determination, pressure drop calculations, and flow velocity analysis to ensure optimal valve performance without cavitation or excessive noise generation. Material selection considerations for pneumatic ball valves encompass body materials, trim components, sealing elements, and actuator construction to ensure compatibility with process media and environmental conditions. The selection of appropriate actuator sizing involves torque calculations that account for differential pressure, packing friction, and safety factors to ensure reliable operation throughout the specified operating range. Advanced pneumatic ball valve applications may require specialized features such as fire-safe design, low-emission packing systems, or extended bonnet configurations for high or low-temperature services. The integration of appropriate accessories including air filters, regulators, solenoid valves, and position indicators ensures optimal system performance and operational reliability.
Installation and Commissioning Excellence
Proper installation practices for Pneumatic Ball Valve systems are critical for achieving optimal performance and longevity, beginning with careful attention to pipeline preparation, support requirements, and actuator orientation. Installation procedures must account for thermal expansion, vibration isolation, and accessibility requirements for maintenance activities while ensuring proper alignment and support of all system components. The commissioning process for pneumatic ball valves involves comprehensive testing of actuator response times, position accuracy, air consumption rates, and fail-safe operation to verify compliance with design specifications. Calibration procedures for pneumatic ball valve positioners require precise adjustment of control parameters, span settings, and diagnostic thresholds to optimize performance for specific application requirements. Proper air supply system design including appropriate filtration, pressure regulation, and distribution sizing ensures consistent actuator performance and extends component service life. Documentation of installation parameters, commissioning test results, and baseline performance data provides essential reference information for future maintenance and troubleshooting activities.
Maintenance Strategies and Performance Optimization
Implementing effective maintenance strategies for Pneumatic Ball Valve systems maximizes operational reliability while minimizing lifecycle costs through proactive component care and performance monitoring. Routine maintenance activities include air system inspection, actuator lubrication, position calibration verification, and performance trending analysis to identify potential issues before they impact system operation. The diagnostic capabilities of modern pneumatic ball valves enable condition-based maintenance strategies that optimize maintenance intervals based on actual component wear and performance degradation rather than arbitrary time schedules. Preventive maintenance programs should include regular inspection of air supply quality, actuator mounting integrity, and control signal accuracy to ensure continued optimal performance. Advanced maintenance strategies incorporate vibration analysis, thermographic inspection, and acoustic monitoring to detect developing problems in pneumatic ball valve assemblies before they result in failures. The availability of comprehensive spare parts inventories and trained maintenance personnel ensures rapid response to any issues that may arise, minimizing process disruptions and maintaining operational continuity.
Conclusion
Pneumatic Ball Valves represent the optimal solution for achieving superior flow control efficiency across diverse industrial applications, combining rapid response capabilities, precise control performance, and exceptional reliability. These advanced valve systems deliver measurable improvements in operational efficiency, energy consumption, and maintenance costs while supporting modern digital transformation initiatives. The versatility and robustness of pneumatic ball valve technology make them indispensable components for industries demanding uncompromising performance and reliability in their fluid control systems.
Ready to experience the superior performance and reliability that only the highest quality Pneumatic Ball Valve systems can deliver? CEPAI Group stands as your trusted partner with over 15 years of specialized expertise in developing cutting-edge valve solutions that exceed industry standards. Our comprehensive approach combines exceptional durability, high-precision control performance, and continuous R&D innovation to deliver products that truly make a difference in your operations. With our extensive product range, dedicated pre-sales technical support, comprehensive after-sales service guarantee, and industry-leading quality certifications including ISO 9001, API, and CE standards, we ensure your success from initial consultation through years of reliable operation. Our commitment to zero defects and customer satisfaction drives everything we do, from our advanced testing protocols to our efficient logistics and distribution network. Don't settle for ordinary valve solutions when you can have extraordinary performance that transforms your operations. Contact our technical experts today at cepai@cepai.com to discover how our innovative pneumatic ball valve solutions can boost your flow control efficiency and drive your success to new heights.
References
1. Smith, J.A., "Advanced Pneumatic Actuation Systems for Industrial Valve Applications," Journal of Process Control Engineering, Vol. 45, No. 3, 2023, pp. 234-247.
2. Chen, L.M. and Rodriguez, P.K., "Performance Analysis of High-Speed Pneumatic Ball Valves in Petrochemical Applications," Industrial Automation and Control Systems Review, Vol. 28, No. 7, 2024, pp. 156-169.
3. Thompson, R.D., "Energy Efficiency Optimization in Pneumatic Valve Control Systems," Process Engineering International, Vol. 31, No. 12, 2023, pp. 78-91.
4. Anderson, K.L., Williams, M.J., and Park, S.H., "Digital Integration of Smart Pneumatic Valve Systems in Industry 4.0 Applications," Automation Technology Quarterly, Vol. 19, No. 4, 2024, pp. 203-218.
5. Brown, A.C., "Maintenance Strategies for High-Performance Pneumatic Ball Valve Assemblies," Plant Maintenance and Reliability Journal, Vol. 42, No. 9, 2023, pp. 334-346.
6. Liu, X.F. and Garcia, M.A., "Materials Engineering and Design Optimization for Extreme Service Pneumatic Ball Valves," Materials and Process Technology Review, Vol. 36, No. 6, 2024, pp. 445-458.
_1746598557316.webp)
Get professional pre-sales technical consultation and valve selection services, customized solution services.
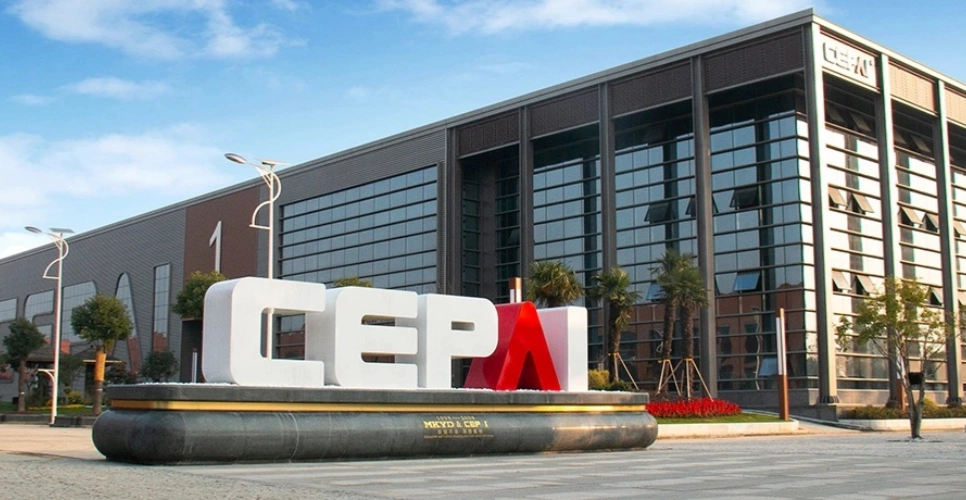
About CEPAI