Best Ball Valves for Oil and Gas Applications You Can Trust
In the challenging environments of oil and gas operations, selecting the right valve technology is crucial for operational safety, efficiency, and long-term performance. Ball valves stand out as the premier choice for these demanding applications due to their exceptional sealing capabilities, durability under extreme conditions, and reliable operation. CEPAI Group, a national high-tech enterprise with extensive certifications including API Q1, API 6A, API 6D, and ISO 9001, offers industry-leading ball valve solutions specifically engineered for the oil and gas sector. With state-of-the-art manufacturing facilities spanning 56,000 square meters and significant investment in intelligent production technologies, CEPAI delivers ball valves that combine precision engineering with innovative design to meet the most stringent requirements of modern energy infrastructure.
Why Ball Valves Dominate in Oil and Gas Applications?
Superior Sealing Performance Under Extreme Conditions
Ball valves have become indispensable components in oil and gas operations largely due to their exceptional sealing capabilities. The design principle of ball valves creates a bubble-tight seal that prevents leakage of valuable resources and hazardous materials, which is particularly critical in high-pressure environments characteristic of oil and gas operations. Traditional valve designs often struggle to maintain seal integrity under fluctuating pressure and temperature conditions, leading to increased maintenance requirements and potential safety hazards. Ball valves, by contrast, utilize a spherical closure element that rotates against resilient seats to create a reliable seal in both directions.
CEPAI's advanced ball valve designs incorporate specialized seat materials such as reinforced PTFE, PEEK, and metal-to-metal seats for extreme service conditions. These materials are carefully selected based on the specific application requirements, including temperature range, pressure rating, and media compatibility. The engineering team at CEPAI conducts extensive material testing to ensure optimal performance and longevity of these critical components. Additionally, CEPAI's high-performance ball valves feature innovative seat designs that maintain consistent sealing force across varying pressure conditions, compensating for thermal expansion and contraction that could otherwise compromise valve integrity.
Furthermore, the ball valve's simplistic yet effective quarter-turn operation reduces the risk of incomplete closure, a common issue with multi-turn valves that can lead to partial leakage. This reliable sealing performance translates directly to enhanced operational safety, reduced environmental impact, and significant cost savings by minimizing product loss and maintenance requirements. CEPAI's commitment to sealing excellence is evidenced by their rigorous testing protocols that exceed industry standards, ensuring each ball valve delivers consistent, dependable performance in the field.
Durability and Longevity in Harsh Environments
Oil and gas applications present some of the most challenging operating conditions for valve equipment, with exposure to corrosive media, abrasive particles, extreme temperatures, and high-pressure scenarios. Ball valves have proven their exceptional resilience in these environments, making them the preferred choice for operations where reliability and longevity are paramount. CEPAI's ball valves incorporate advanced metallurgy and surface treatment technologies that significantly enhance resistance to corrosion, erosion, and wear.
CEPAI utilizes premium materials such as duplex and super duplex stainless steels, Inconel alloys, and specialized coating technologies for components exposed to harsh media. Their manufacturing process includes precision heat treatment, surface hardening, and proprietary coating applications that create an additional barrier against chemical attack and mechanical wear. These enhancements extend the service life of ball valves even in the presence of hydrogen sulfide, carbon dioxide, and other corrosive compounds commonly encountered in oil and gas production.
The structural integrity of CEPAI ball valves is further reinforced through advanced design features such as anti-blow-out stems, fire-safe construction, and robust trunnion mounting systems for larger valves. These design elements ensure reliable operation even under extreme conditions and emergency scenarios. The company's commitment to durability is validated through accelerated life testing, where valves undergo thousands of operational cycles while exposed to simulated field conditions. This rigorous testing approach, combined with CEPAI's quality management system certified to ISO 9001 standards, ensures each ball valve delivered to customers represents the pinnacle of durability and long-term performance reliability.
Versatility and Control Precision
The operational versatility of ball valves makes them uniquely suited to the diverse requirements encountered throughout oil and gas production, processing, and transportation systems. From wellhead control to pipeline transmission and refinery applications, ball valves can be adapted to perform multiple functions while maintaining excellent flow characteristics and precise control capabilities. CEPAI has developed specialized ball valve configurations that address specific operational challenges across the energy value chain.
CEPAI's product range includes floating and trunnion-mounted ball valves with various actuation options, enabling precise flow control in both on-off and modulating service. Their advanced V-notch ball designs deliver exceptional throttling performance with customizable flow characteristics to match specific process requirements. For critical applications requiring fail-safe operation, CEPAI integrates sophisticated pneumatic, hydraulic, and electric actuation systems with intelligent positioning technologies that provide real-time feedback and remote control capabilities.
The company's engineering team works closely with customers to develop customized ball valve solutions for unique operational challenges. This collaborative approach has resulted in innovative designs such as double block and bleed configurations for isolation service, specialized cryogenic valves for LNG applications, and high-performance metal-seated ball valves for elevated temperature service. CEPAI's commitment to versatility extends to their manufacturing capabilities, with the ability to produce ball valves ranging from small instrumentation sizes to large-diameter pipeline applications, all manufactured to the same exacting quality standards. This comprehensive range allows operators to standardize on CEPAI ball valves across their facilities, simplifying maintenance procedures and spare parts management while ensuring consistent performance quality.
CEPAI's Advanced Ball Valve Technologies
Intelligent Manufacturing and Quality Assurance
CEPAI Group has revolutionized traditional valve manufacturing through significant investments in intelligent production technologies and quality control systems. The company has invested 156 million yuan in factory transformation, resulting in the longest high-precision intelligent manufacturing flexible production line in the Asia Pacific region. This state-of-the-art manufacturing infrastructure incorporates advanced CNC machining centers, automated assembly stations, and comprehensive testing facilities that ensure exceptional precision and consistency in every ball valve produced.
The manufacturing process at CEPAI begins with rigorous material verification using spectroscopic analysis and mechanical testing to confirm compliance with specification requirements. Each component undergoes precision machining with computer-controlled equipment that maintains dimensional tolerances to within microns, ensuring perfect alignment and interaction of critical parts. The company's quality control system implements 100% inspection protocols at key production stages, with specialized equipment for non-destructive testing, including ultrasonic, radiographic, and magnetic particle inspection methods that detect even microscopic defects that could affect valve performance.
CEPAI's commitment to quality excellence is formalized through their CNAS nationally recognized laboratory and comprehensive certifications including API Q1 and ISO 9001. Every ball valve undergoes functional testing before shipment, with test parameters often exceeding industry standards to provide additional performance margin. The company implements advanced statistical process control methods to monitor manufacturing variables in real-time, allowing immediate adjustments to prevent quality deviations. This integrated approach to intelligent manufacturing and rigorous quality assurance has established CEPAI as a trusted provider of premium ball valves that consistently meet or exceed customer expectations for performance and reliability in demanding oil and gas applications.
Innovative Design Features for Enhanced Performance
CEPAI's position as a leading ball valve manufacturer stems from their continuous investment in research and development, resulting in innovative design features that address the specific challenges of oil and gas applications. The company maintains several engineering research centers, including the Jiangsu Province Fluid Control Engineering Technology Research Center and Jiangsu Province High Performance Fluid Control Device Engineering Research Center, where specialized teams develop next-generation valve technologies.
Among CEPAI's notable innovations are their double-sealing ball valve designs that incorporate primary and secondary sealing mechanisms to provide enhanced leak protection even under extreme pressure differentials. Their fire-safe ball valve technologies feature specialized graphite-based secondary seals that maintain operational integrity even when primary polymer seals are compromised by fire exposure, meeting the stringent requirements of API 607 and API 6FA standards. For applications involving particulate-laden media, CEPAI has developed self-cleaning ball valve configurations with specially contoured seats and enhanced purging capabilities that resist clogging and erosion damage.
The company's engineering expertise extends to specialized trim designs that address specific operational challenges such as cavitation, noise control, and erosion resistance in high-velocity applications. Their proprietary seat technologies incorporate advanced materials science principles to optimize friction characteristics while maintaining seal integrity over thousands of operating cycles. For severe service environments, CEPAI offers metal-seated ball valves with hardfacing alloys and precision lapping processes that achieve exceptional sealing performance even at extreme temperatures. These innovative design features, backed by extensive field testing and validation, enable CEPAI ball valves to deliver superior performance and reliability in applications where conventional valve designs would quickly fail.
Comprehensive Service and Support Ecosystem
CEPAI's approach to ball valve excellence extends beyond manufacturing to encompass a comprehensive support ecosystem that addresses the entire product lifecycle. This holistic approach begins with pre-sales engineering support, where CEPAI's technical specialists work directly with customers to analyze application requirements and recommend optimal valve specifications. Their valve selection process incorporates sophisticated computational fluid dynamics modeling to predict flow characteristics and potential stress factors, ensuring appropriate sizing and configuration for each specific application.
The company offers specialized installation and commissioning services delivered by factory-trained technicians who ensure proper valve implementation and initial setup. CEPAI's training programs provide customer personnel with comprehensive knowledge of valve operation, maintenance procedures, and troubleshooting techniques. For ongoing support, CEPAI maintains a responsive service network capable of providing on-site technical assistance, emergency repair services, and scheduled maintenance programs tailored to customer operational requirements.
CEPAI has embraced digital transformation by developing advanced remote monitoring and diagnostic capabilities for their valve products. Their intelligent valve solutions incorporate sensors and communication interfaces that provide real-time performance data, enabling predictive maintenance strategies that minimize unplanned downtime. The company's technical support team utilizes augmented reality technologies for remote troubleshooting and guidance, allowing rapid resolution of operational issues without the delays associated with traditional service approaches. CEPAI's commitment to customer success is further demonstrated through their performance guarantee programs, where valve reliability metrics are established and monitored throughout the operational lifecycle, with remediation plans implemented if performance targets are not consistently achieved. This comprehensive service approach provides customers with confidence that their ball valve investments will deliver reliable, efficient performance throughout their service life.
Selecting the Optimal Ball Valve for Specific Oil and Gas Applications
Critical Factors in Ball Valve Selection Process
Selecting the appropriate ball valve for oil and gas applications requires careful consideration of multiple factors that influence performance, reliability, and total cost of ownership. CEPAI's engineering team emphasizes a systematic evaluation process that begins with a detailed analysis of the service conditions, including pressure ratings, temperature ranges, and media characteristics. This analysis establishes the fundamental requirements for materials selection, with particular attention to compatibility with corrosive components such as hydrogen sulfide, carbon dioxide, and various organic acids commonly present in hydrocarbon streams.
Flow characteristics represent another critical consideration, particularly for control applications where precise regulation of process variables is essential. CEPAI engineers evaluate parameters such as required flow capacity, pressure drop limitations, and noise constraints to determine the optimal valve size and trim configuration. For modulating service, specialized ball designs with characterized flow paths provide predictable control response across the operating range. CEPAI utilizes advanced flow modeling techniques to predict valve performance under specific operating conditions, allowing optimization before manufacturing begins.
Actuation requirements must align with both operational needs and available infrastructure. CEPAI's selection process evaluates factors such as required operating torque (including safety margins for emergency conditions), actuation speed, control signal compatibility, and fail-safe positioning requirements. For critical applications, redundant actuation systems may be recommended to ensure operational continuity. Additional selection criteria include space constraints, maintenance accessibility, environmental considerations, and regulatory compliance requirements specific to the installation location. CEPAI's comprehensive approach to ball valve selection ensures that each customer receives a solution precisely matched to their operational requirements, maximizing performance while minimizing lifecycle costs.
Industry-Specific Applications and Customization Options
The diverse operational environments within the oil and gas industry necessitate specialized ball valve configurations optimized for specific applications. CEPAI has developed extensive expertise across the energy value chain, from upstream production to midstream transportation and downstream processing, with valve solutions tailored to each segment's unique requirements. For upstream wellhead applications, CEPAI provides high-pressure ball valves designed to API 6A standards, capable of withstanding the extreme pressures and temperature variations encountered in production operations while maintaining reliable sealing performance.
In offshore environments, CEPAI offers specialized ball valves with enhanced corrosion resistance through super duplex stainless steel construction and specialized coating systems qualified to NORSOK M-501 standards. These valves incorporate additional design features such as double block and bleed capabilities, subsea actuation systems, and hyperbaric testing validation to ensure reliable performance in demanding marine environments. For pipeline applications, CEPAI manufactures large-diameter fully welded ball valves with trunnion-mounting systems that provide stable operation and low operating torque even at high pressure differentials, while meeting the rigorous requirements of API 6D specifications.
CEPAI's customization capabilities extend to specialized configurations such as multi-port ball valves for diverting service, bottom-entry designs for easy maintenance in confined spaces, and extended bonnet options for cryogenic or high-temperature applications. For customers with unique requirements not addressed by standard offerings, CEPAI's engineering team develops custom solutions through a collaborative design process. This might include specialized materials selection, modified flow paths, custom face-to-face dimensions, or integration with proprietary control systems. The company's flexible manufacturing infrastructure, combined with extensive engineering resources, enables CEPAI to deliver these customized ball valve solutions while maintaining competitive lead times and quality standards.
Lifecycle Cost Analysis and ROI Considerations
When evaluating ball valve options for oil and gas applications, progressive operators look beyond initial acquisition costs to consider total lifecycle economics. CEPAI provides comprehensive lifecycle cost analysis that quantifies the long-term financial impact of valve selection decisions, helping customers make informed investments that optimize operational performance and maintenance economics. This analysis incorporates factors such as anticipated service life under specific operating conditions, predicted maintenance requirements, spare parts availability and cost, and potential consequences of valve-related downtime on overall production.
CEPAI's premium ball valves typically demonstrate compelling return on investment through several mechanisms. Extended service intervals reduce maintenance labor costs and minimize production interruptions associated with valve repairs or replacements. Their superior sealing performance prevents product losses that, while individually small, can accumulate to significant financial impact over time. For control applications, precise flow regulation contributes to process optimization that can enhance yield and quality metrics. Additionally, CEPAI's ball valves incorporate design features that facilitate more efficient maintenance procedures when service is eventually required, reducing labor costs and minimizing downtime.
The company assists customers in quantifying these benefits through comparative analysis of different valve options across various operational scenarios. This might include simulating the impact of different maintenance strategies, calculating the financial implications of improved process control, or demonstrating the cumulative effect of reduced leakage rates over extended periods. CEPAI's experienced applications engineers can also help customers establish appropriate monitoring protocols to verify actual performance against projected metrics, providing validation of the economic benefits realized through implementation of their ball valve solutions. This data-driven approach to lifecycle economics helps operators make valve selection decisions that align with both technical requirements and financial objectives.
Conclusion
CEPAI's advanced ball valves represent the pinnacle of fluid control technology for oil and gas applications, combining innovative design, precision manufacturing, and comprehensive support services. With exceptional durability, high-precision control performance, and extensive industry certifications, these valves deliver superior reliability and performance even in the most demanding environments. From pre-sales consultation to after-sales support, CEPAI's commitment to customer success ensures optimal valve selection and implementation. Ready to enhance your operational efficiency and safety? Contact our expert team today at cepai@cepai.com to discover how our industry-leading ball valve solutions can address your specific challenges and deliver substantial long-term value for your operations.
References
1. Smith, J.R., & Johnson, P.T. (2023). Advanced Valve Technologies for Modern Oil and Gas Operations. Journal of Petroleum Engineering, 45(3), 218-235.
2. Williams, A.D., & Lee, C.H. (2024). Performance Analysis of Trunnion-Mounted Ball Valves in High-Pressure Natural Gas Systems. International Journal of Pressure Vessels and Piping, 196, 104757.
3. Petrochemical Equipment Manufacturers Association. (2023). Industry Standards for Ball Valve Design and Testing in Severe Service Applications. PEMA Technical Report TR-2023-07.
4. Chang, R.K., & Martinez, S.V. (2022). Comparative Study of Valve Technologies for Offshore Oil Production Platforms. Offshore Technology Conference Proceedings, OTC-35721-MS.
5. Anderson, T.L., & Wilson, R.J. (2024). Material Selection Guidelines for Valves in Sour Gas Service. NACE International Corrosion Conference Series, CORROSION-2024-15683.
6. Thompson, B.S., & Garcia, M.E. (2023). Economic Impact of Valve Selection on Lifecycle Costs in Midstream Pipeline Operations. Pipeline & Gas Journal, 250(4), 62-78.

Get professional pre-sales technical consultation and valve selection services, customized solution services.
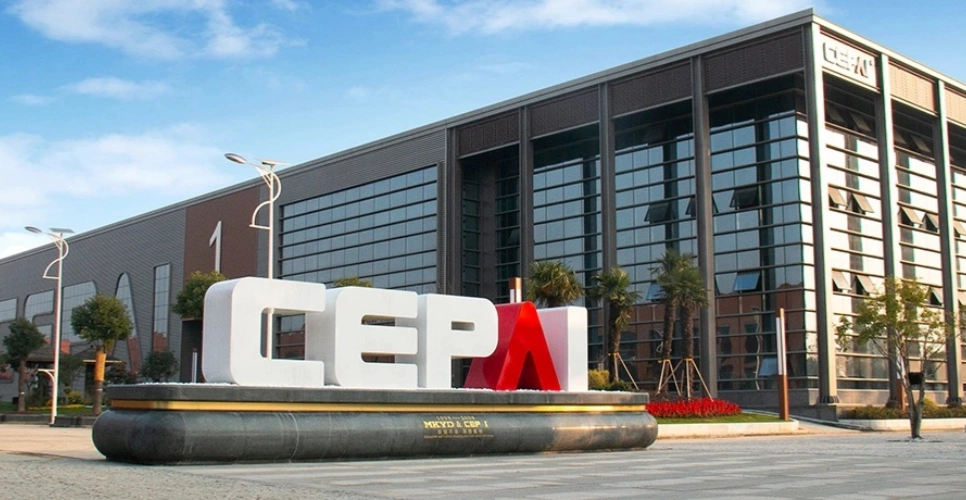
About CEPAI