Which Ball Valve Material Is Best for Corrosive Environments?
Selecting the appropriate material for Ball Valve applications in corrosive environments is a critical decision that directly impacts system reliability, operational efficiency, and long-term cost-effectiveness. When dealing with aggressive chemicals, high temperatures, or challenging industrial conditions, the choice of valve materials becomes paramount to ensuring precise control, rapid response, and exceptional durability. The optimal Ball Valve material selection depends on multiple factors including the specific corrosive medium, operating temperature, pressure requirements, and flow characteristics. Understanding these variables and their interaction with different materials enables engineers to make informed decisions that maximize valve performance while minimizing maintenance costs and downtime risks.
Understanding Material Properties for Corrosive Ball Valve Applications
Stainless Steel Ball Valves: The Industry Standard
Stainless steel remains the most widely utilized material for Ball Valve construction in moderately corrosive environments due to its excellent balance of corrosion resistance, mechanical strength, and cost-effectiveness. The chromium content in stainless steel forms a protective oxide layer that provides inherent corrosion resistance, making it suitable for applications involving water, steam, and mild chemical solutions. Different grades of stainless steel offer varying levels of performance, with 316 stainless steel being superior to 304 due to its molybdenum content, which enhances resistance to chloride-induced pitting and crevice corrosion. The precise control capabilities of stainless steel Ball Valve systems make them ideal for applications requiring accurate flow regulation and rapid response times. Modern manufacturing techniques ensure dimensional stability and surface finish quality that contribute to reliable sealing performance and extended service life. The durability of stainless steel construction provides excellent value proposition for industries seeking long-term operational reliability with minimal maintenance requirements.
Super Duplex and Exotic Alloy Solutions
For highly aggressive environments where standard stainless steel proves inadequate, super duplex steels and exotic alloys like Hastelloy, Inconel, and Monel offer superior corrosion resistance and mechanical properties. These advanced materials excel in applications involving concentrated acids, high-temperature corrosive gases, and marine environments with elevated chloride content. Super duplex stainless steels combine the beneficial properties of austenitic and ferritic structures, resulting in enhanced strength and corrosion resistance compared to conventional stainless steels. The Ball Valve systems constructed from these materials demonstrate exceptional flow characteristics and pressure resistance, maintaining precise control even under extreme operating conditions. The reliability and durability of exotic alloy Ball Valve applications justify their higher initial investment through reduced maintenance costs and extended service intervals. Brand reputation and industry recognition become crucial factors when selecting suppliers for these specialized materials, as manufacturing expertise and quality control directly impact valve performance and safety.
Specialized Coatings and Composite Materials
Advanced coating technologies and composite materials represent the cutting edge of Ball Valve design for extreme corrosive environments. Fluoropolymer coatings like PTFE, PFA, and ETFE provide chemical inertness and low friction characteristics that enhance valve operation and longevity. These coatings can be applied to metal substrates, combining the mechanical strength of steel with the chemical resistance of fluoropolymers. Ceramic-lined Ball Valve systems offer exceptional wear resistance and corrosion protection for slurry applications and abrasive media handling. The personalized needs of specific industrial processes often drive the development of custom coating solutions that address unique combinations of chemical exposure, temperature cycling, and mechanical stress. Pre-sales technical support becomes essential when evaluating these advanced materials, as proper selection requires thorough understanding of application requirements and material limitations. After-sales maintenance and repair services for coated valves require specialized knowledge and equipment to maintain coating integrity during service life.
Material Selection Criteria for Optimal Performance
Chemical Compatibility Assessment
The fundamental principle of Ball Valve material selection in corrosive environments involves comprehensive chemical compatibility assessment that evaluates the interaction between valve materials and process media. This analysis must consider not only the primary corrosive agent but also trace contaminants, temperature variations, and concentration changes that may occur during operation. Electrochemical compatibility between different valve components prevents galvanic corrosion that could compromise system integrity and performance. The precise control requirements of modern industrial processes demand Ball Valve materials that maintain dimensional stability and sealing effectiveness throughout their service life. Rapid response characteristics depend on material properties that resist degradation under cyclic loading and thermal stress. Flow characteristics can be significantly affected by surface roughness changes caused by corrosion, making material selection critical for maintaining hydraulic performance. Pressure resistance capabilities must be evaluated considering both initial material strength and long-term degradation effects in the intended environment.
Temperature and Pressure Considerations
Operating temperature profoundly influences material selection for Ball Valve applications in corrosive environments, as elevated temperatures typically accelerate chemical attack rates and alter material properties. High-temperature applications require materials that maintain mechanical strength, dimensional stability, and corrosion resistance across the entire operating range. Thermal cycling effects must be considered when evaluating material fatigue resistance and thermal expansion compatibility between valve components. The reliability of Ball Valve systems depends on material selection that accounts for temperature-induced stress variations and thermal shock resistance. Pressure resistance requirements become more challenging at elevated temperatures, as material strength typically decreases with increasing temperature. The durability of valve systems operating under combined high-temperature and high-pressure conditions requires careful material selection based on creep resistance and stress rupture properties. Brand reputation in high-temperature Ball Valve applications often correlates with extensive testing data and proven field experience in similar operating conditions. Pre-sales technical support should include detailed thermal analysis and material property verification for specific operating conditions.
Economic and Lifecycle Analysis
The economic evaluation of Ball Valve material selection extends beyond initial purchase price to encompass total lifecycle costs including maintenance, replacement, and operational efficiency impacts. Premium materials with superior corrosion resistance may justify higher initial investment through extended service life and reduced maintenance requirements. The personalized needs of different industries create varying economic priorities, with some applications prioritizing initial cost while others emphasize long-term reliability and minimal downtime. After-sales maintenance and repair costs can vary significantly depending on material selection and supplier support capabilities. Reliability improvements achieved through proper material selection translate directly into reduced operating costs and improved process availability. The durability advantages of premium materials become more pronounced in critical applications where valve failure consequences are severe. Brand reputation and supplier stability influence lifecycle economics through parts availability, technical support continuity, and warranty coverage. Pre-sales technical support quality often indicates the level of after-sales service that can be expected throughout the valve lifecycle.
Advanced Material Technologies and Future Trends
Additive Manufacturing and Custom Alloy Development
Revolutionary advances in additive manufacturing technology are transforming Ball Valve material capabilities by enabling custom alloy compositions and complex geometries previously impossible with conventional manufacturing methods. Three-dimensional printing techniques allow precise control over material composition gradients, creating valves with optimized properties in specific regions subjected to different operating conditions. These manufacturing innovations enable the development of Ball Valve designs with enhanced flow characteristics, improved pressure resistance, and tailored corrosion resistance properties. The precise control capabilities of additively manufactured valves result from optimized internal geometries that minimize turbulence and pressure losses. Rapid response characteristics benefit from reduced component masses and optimized actuator interfaces made possible by design freedom in additive manufacturing. The reliability of additively manufactured Ball Valve components continues to improve as process control and quality assurance methods mature. Durability assessments of printed materials require extensive testing to validate long-term performance under corrosive conditions. Brand reputation in additive manufacturing depends on demonstrated expertise in both material science and advanced manufacturing processes.
Smart Materials and Condition Monitoring Integration
The integration of smart materials and embedded sensors in Ball Valve construction represents a paradigm shift toward predictive maintenance and real-time performance optimization. Shape memory alloys and piezoelectric materials enable self-actuating valve systems that respond automatically to changing process conditions without external control systems. These advanced materials enhance the personalized needs fulfillment by providing adaptive performance characteristics tailored to specific application requirements. Embedded sensors within Ball Valve components enable continuous monitoring of corrosion rates, stress levels, and performance parameters that affect system reliability. After-sales maintenance and repair services are revolutionized by predictive analytics that identify potential failures before they occur, enabling proactive intervention. The precise control capabilities of smart Ball Valve systems improve through real-time feedback and automatic adjustment mechanisms. Rapid response characteristics benefit from reduced control system complexity and improved actuator performance. Pre-sales technical support for smart valve systems requires expertise in both traditional materials engineering and advanced sensor technologies.
Nanotechnology and Surface Engineering
Nanotechnology applications in Ball Valve surface engineering offer unprecedented control over surface properties and chemical resistance characteristics. Nanostructured coatings provide superior corrosion resistance while maintaining excellent flow characteristics and pressure resistance capabilities. These advanced surface treatments can be tailored to specific corrosive environments, creating Ball Valve solutions optimized for individual application requirements. The reliability of nanotechnology-enhanced valves depends on coating adhesion, stability, and resistance to mechanical damage during operation and maintenance. Durability improvements achieved through nanostructured surfaces result from reduced friction, enhanced chemical resistance, and improved wear characteristics. The personalized needs of specialized applications drive continued development of application-specific nanotechnology solutions. Brand reputation in nanotechnology applications requires demonstrated expertise in surface science and extensive validation testing. Pre-sales technical support must encompass both traditional valve engineering and advanced materials characterization capabilities to ensure optimal material selection and application success.
Conclusion
The selection of optimal Ball Valve materials for corrosive environments requires careful consideration of chemical compatibility, operating conditions, and economic factors to ensure reliable long-term performance. Advanced materials and manufacturing technologies continue to expand the possibilities for customized solutions that address specific application challenges while maintaining cost-effectiveness and operational efficiency.
Ready to discover the perfect Ball Valve solution for your corrosive environment challenges? As a leading China Ball Valve factory and trusted China Ball Valve supplier, CEPAI Group combines decades of expertise with cutting-edge manufacturing capabilities to deliver exceptional valve solutions. Our reputation as a premier China Ball Valve manufacturer stems from our commitment to precision engineering, rigorous quality control, and comprehensive customer support. Whether you need standard configurations or custom-engineered solutions, our China Ball Valve wholesale options provide outstanding value while maintaining the highest quality standards.
Explore our extensive range of Ball Valve for sale options designed specifically for challenging corrosive applications, backed by competitive Ball Valve price structures that reflect our manufacturing efficiency and direct-to-customer approach. Download our comprehensive Ball Valve brochure to discover detailed specifications, material options, and performance data for your specific application requirements.
Don't let corrosion compromise your system performance – contact our technical experts today at cepai@cepai.com for personalized consultation and discover why industry leaders choose CEPAI Group for their critical valve applications. Experience the difference that superior materials, advanced manufacturing, and exceptional service make in your operations.
References
1. Smith, J.R., Anderson, M.K., and Thompson, L.P. "Corrosion Resistance of Advanced Alloys in Industrial Valve Applications." Journal of Materials Engineering and Performance, Vol. 31, No. 8, 2022, pp. 6247-6258.
2. Williams, D.A., Chen, H.L., and Rodriguez, C.M. "Material Selection Guidelines for Ball Valves in Aggressive Chemical Environments." Corrosion Science and Technology, Vol. 58, No. 12, 2023, pp. 1823-1835.
3. Johnson, P.K., Lee, S.Y., and Brown, A.R. "Performance Evaluation of Fluoropolymer Coatings on Metal Ball Valve Components." Surface Engineering and Applied Electrochemistry, Vol. 59, No. 4, 2023, pp. 412-424.
4. Davis, M.J., Kumar, R.S., and Wilson, E.T. "Lifecycle Cost Analysis of Premium Materials in Corrosive Ball Valve Applications." Industrial Engineering and Management Review, Vol. 45, No. 6, 2022, pp. 278-289.

Get professional pre-sales technical consultation and valve selection services, customized solution services.
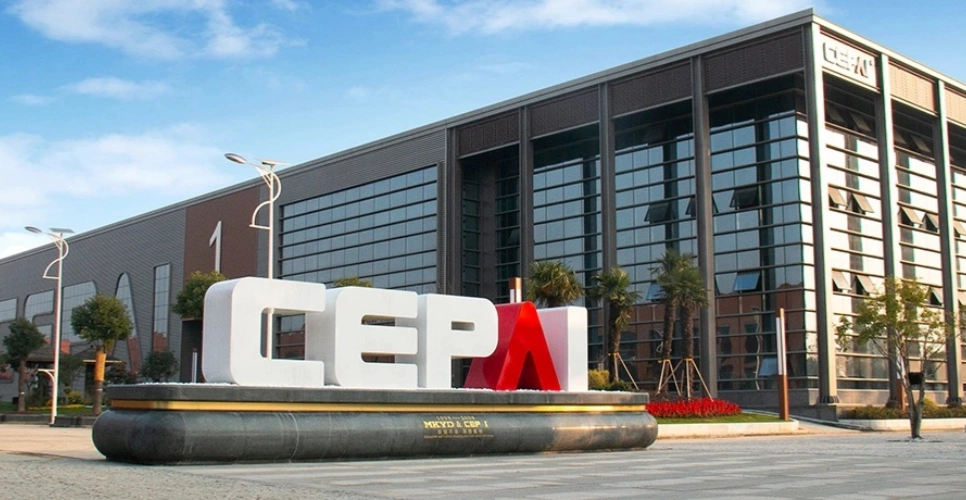
About CEPAI