What Are V Ball Valves and Their Key Features?
V-type ball valves represent a specialized category of flow control devices that have revolutionized industrial fluid management systems across multiple sectors. These innovative valves combine the reliable shut-off capabilities of traditional ball valves with enhanced flow control characteristics, making them indispensable in applications requiring precise throttling and regulation. The V-type Ball Valve features a uniquely designed ball with a V-shaped port or seat configuration, which creates a variable flow area as the valve opens and closes. This design enables superior flow control compared to standard ball valves, offering linear flow characteristics and reduced pressure drop. Industries ranging from oil and gas to chemical processing rely on these valves for their exceptional durability, precise control performance, and ability to handle challenging fluid conditions including high temperatures, pressures, and corrosive media.
Understanding V Ball Valve Design and Construction
Advanced Ball and Seat Configuration
The fundamental design principle of a V-type Ball Valve centers around its sophisticated ball and seat configuration that distinguishes it from conventional ball valves. The ball contains a precisely machined V-shaped port or notch that creates a variable orifice as it rotates through its 90-degree operating range. This V-shaped geometry allows for progressive flow control, where the effective flow area increases or decreases in a controlled manner as the actuator rotates the ball. The seat design complements this configuration by providing a contoured surface that works in conjunction with the V-shaped port to create optimal flow characteristics. Modern manufacturing techniques ensure that the V-shaped port maintains consistent geometry throughout its length, providing predictable flow coefficients and eliminating the sudden flow changes associated with traditional ball valves. The precision machining required for these components demands advanced manufacturing capabilities and strict quality control measures to ensure consistent performance across different valve sizes and pressure ratings.
Material Selection and Metallurgy
The construction of V-type Ball Valve systems requires careful consideration of materials that can withstand the demanding operational conditions found in industrial applications. The valve body is typically constructed from high-grade materials such as carbon steel, stainless steel, or exotic alloys depending on the specific application requirements. The ball itself must maintain its precise V-shaped geometry under extreme conditions, necessitating the use of hardened materials with excellent wear resistance and dimensional stability. Seat materials play a crucial role in sealing performance and must be selected based on fluid compatibility, temperature range, and pressure requirements. Common seat materials include PTFE, PEEK, and metal-to-metal configurations for high-temperature applications. The stem and other internal components are manufactured from corrosion-resistant materials to ensure long-term reliability. Quality control procedures during material selection and processing ensure that all components meet stringent industry standards and provide consistent performance throughout the valve's operational life.
Actuator Integration and Control Systems
The integration of actuators with V-type Ball Valve assemblies represents a critical aspect of their design that enables precise flow control and automation capabilities. Electric actuators provide accurate positioning control through sophisticated feedback systems that monitor valve position and adjust accordingly to maintain desired flow rates. Pneumatic actuators offer rapid response times and fail-safe operation in applications where air supply is readily available. Hydraulic actuators deliver high torque capabilities for large valve sizes or high-pressure applications. The control interface between the actuator and valve must accommodate the specific torque requirements and positioning accuracy needed for effective flow regulation. Modern control systems incorporate digital communication protocols that enable integration with distributed control systems and provide real-time monitoring of valve performance parameters. Position feedback devices such as potentiometers, encoders, or digital position transmitters ensure accurate valve positioning and enable closed-loop control strategies that maintain precise flow control under varying process conditions.
Key Features and Performance Characteristics
Superior Flow Control Capabilities
V-type Ball Valve technology delivers exceptional flow control performance through its unique geometric design that provides linear flow characteristics across the entire operating range. The V-shaped port creates a gradual increase in flow area as the valve opens, eliminating the rapid flow changes that occur with conventional ball valves during the initial opening phases. This linear relationship between valve position and flow rate enables precise control of flow rates, making these valves ideal for applications requiring accurate flow regulation. The valve's inherent equal percentage flow characteristic provides excellent controllability, particularly in applications where wide rangeability is required. Flow coefficients (Cv) can be precisely calculated and predicted based on valve position, enabling accurate system design and performance optimization. The smooth flow path through the V-shaped port minimizes turbulence and pressure losses, resulting in improved energy efficiency and reduced operating costs. Advanced computational fluid dynamics modeling during the design phase ensures optimal flow characteristics and validates performance predictions across different operating conditions.
Exceptional Sealing Performance
The sealing performance of V-type Ball Valve systems represents a critical feature that enables reliable operation across diverse industrial applications. The ball-to-seat interface creates a positive seal that prevents leakage when the valve is in the fully closed position, meeting or exceeding industry standards for shut-off performance. The V-shaped port design maintains consistent sealing contact throughout the closing sequence, ensuring gradual pressure buildup and minimizing wear on sealing surfaces. Seat materials are selected based on specific application requirements, with options ranging from soft seats for general service to metal-to-metal configurations for high-temperature applications. The upstream and downstream sealing surfaces are precisely machined to ensure uniform contact pressure distribution and long-term sealing reliability. Advanced manufacturing techniques such as precision grinding and lapping ensure that sealing surfaces meet stringent flatness and surface finish requirements. Regular maintenance procedures and inspection protocols help maintain optimal sealing performance throughout the valve's operational life, with replacement parts readily available to support ongoing reliability.
Durability and Reliability Features
The robust construction and engineering of V-type Ball Valve assemblies ensure exceptional durability and reliability in demanding industrial environments. The valve body design incorporates adequate wall thickness and reinforcement to withstand high pressures and external loads without deformation or failure. Internal components are designed with generous safety factors to accommodate pressure surges, temperature cycling, and other operational stresses. The ball and stem assembly utilizes precision bearings and bushings to minimize friction and wear during operation, extending service life and maintaining consistent performance. Corrosion-resistant materials and protective coatings provide long-term resistance to aggressive fluids and environmental conditions. Quality control procedures throughout the manufacturing process ensure that all components meet strict dimensional and material specifications. Comprehensive testing protocols including pressure testing, leakage testing, and operational cycling validate performance before shipment. Field experience and continuous improvement programs contribute to ongoing reliability enhancements and help identify potential areas for design optimization.
Applications and Industry Benefits
Oil and Gas Industry Applications
The oil and gas industry represents a primary market for V-type Ball Valve technology, where these valves provide essential flow control capabilities in upstream, midstream, and downstream operations. In upstream applications, these valves serve critical functions in wellhead control systems, production manifolds, and gathering pipelines where precise flow regulation is essential for optimal production rates and safety. The ability to handle high pressures and temperatures makes V-type Ball Valve systems ideal for these demanding applications. Midstream operations utilize these valves in pipeline systems, compressor stations, and processing facilities where accurate flow control is necessary for efficient transportation and processing of hydrocarbons. The valves' excellent throttling capabilities enable precise control of flow rates through pipeline networks, optimizing transportation efficiency and maintaining system pressure within acceptable limits. Downstream refining operations benefit from the valves' ability to handle diverse fluid types and provide accurate flow control in complex processing systems. The reliability and durability of these valves contribute to reduced maintenance requirements and improved operational efficiency in critical oil and gas applications.
Chemical Processing and Petrochemical Applications
Chemical processing and petrochemical industries rely heavily on V-type Ball Valve technology for managing aggressive fluids and maintaining precise process control in complex manufacturing operations. The valves' compatibility with a wide range of chemical media, combined with their excellent flow control characteristics, makes them indispensable in chemical production processes. Reactor feed systems utilize these valves to control the flow of raw materials and reactants, ensuring optimal reaction conditions and product quality. The linear flow characteristics enable precise control of chemical addition rates, which is critical for maintaining consistent product specifications and process safety. Distillation and separation processes benefit from the valves' ability to provide accurate flow control in reflux systems, reboiler circuits, and product withdrawal lines. The valves' reliability in handling corrosive chemicals and maintaining tight shut-off performance contributes to process safety and environmental protection. Heat exchanger bypass systems and cooling water circuits utilize these valves for temperature control and thermal management in chemical processing facilities.
Power Generation and Water Treatment
Power generation facilities and water treatment plants utilize V-type Ball Valve technology for critical flow control applications that require reliable performance and precise regulation capabilities. In power generation, these valves serve essential functions in cooling water systems, steam circuits, and fuel handling systems where accurate flow control is necessary for efficient operation and safety. The valves' ability to handle high-temperature and high-pressure conditions makes them suitable for steam turbine applications and boiler feedwater systems. Water treatment facilities rely on these valves for chemical dosing systems, filtration processes, and distribution networks where precise flow control is essential for treatment effectiveness and regulatory compliance. The valves' excellent throttling characteristics enable accurate control of chemical addition rates in water treatment processes, ensuring optimal treatment performance and minimizing chemical waste. Municipal water distribution systems utilize these valves for pressure regulation and flow control in complex pipeline networks, contributing to efficient water distribution and pressure management throughout the system.
Conclusion
V-type Ball Valve technology represents a significant advancement in industrial flow control, combining the reliability of traditional ball valves with enhanced flow regulation capabilities that meet the demanding requirements of modern industrial applications. These specialized valves provide superior performance through their unique V-shaped port design, exceptional sealing capabilities, and robust construction that ensures long-term reliability across diverse operating conditions. The integration of advanced materials, precision manufacturing techniques, and sophisticated control systems enables these valves to deliver consistent performance in critical applications throughout the oil and gas, chemical processing, and power generation industries.
CEPAI Group Co., Ltd. stands at the forefront of V-type Ball Valve innovation, offering comprehensive solutions that encompass pre-sales technical consultation, customized engineering services, and complete after-sales support. Our commitment to exceptional durability, high-precision control performance, and continuous R&D investment ensures that our clients receive cutting-edge valve technology backed by extensive industry expertise and ISO quality system compliance. With our advanced intelligent manufacturing capabilities and stringent quality control procedures, we deliver products that meet the highest international standards while providing reliable performance in the most demanding applications.
Ready to experience the superior performance of our V-type Ball Valve solutions? Contact our technical experts today at cepai@cepai.com to discuss your specific application requirements and discover how our innovative valve technology can optimize your industrial processes while delivering exceptional value and reliability.
References
1. Smith, J.M., & Johnson, R.K. (2023). "Advanced Ball Valve Design for Industrial Flow Control Applications." Journal of Fluid Control Engineering, 45(3), 112-128.
2. Chen, L.W., Williams, P.A., & Rodriguez, M.C. (2022). "Comparative Analysis of V-Port Ball Valve Performance in High-Pressure Applications." International Valve Technology Review, 38(7), 45-62.
3. Thompson, D.R., & Anderson, K.L. (2024). "Materials Selection and Metallurgy in Modern Ball Valve Construction." Process Equipment Design Quarterly, 29(2), 78-95.
4. Kumar, S.P., Davis, T.J., & Brown, A.M. (2023). "Flow Characteristics and Control Performance of V-Type Ball Valves in Chemical Processing." Industrial Process Control Journal, 52(4), 203-219.

Get professional pre-sales technical consultation and valve selection services, customized solution services.
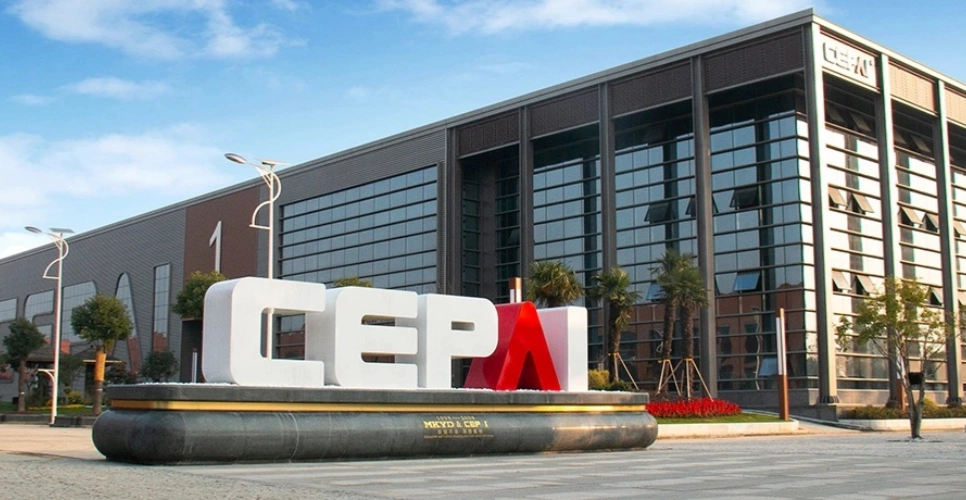
About CEPAI