Understanding 5 Industrial Ball Valve Actuation Methods
Industrial ball valves serve as critical components in fluid control systems across numerous sectors, from petrochemical processing to power generation facilities. The effectiveness of these valves largely depends on their actuation methods, which determine how precisely and reliably they can control fluid flow. Among the various actuation technologies available today, electric ball valve systems have emerged as particularly sophisticated solutions, offering unprecedented levels of automation and control precision. Understanding the five primary actuation methods—manual, pneumatic, hydraulic, electric, and electro-hydraulic—is essential for engineers and procurement professionals seeking optimal valve performance in demanding industrial applications. Each actuation method presents unique advantages in terms of response time, control accuracy, and operational reliability, making the selection process crucial for achieving desired system performance.
Manual Actuation: Foundation of Valve Operation
Manual actuation represents the most fundamental approach to ball valve operation, relying on direct human intervention through handwheels, levers, or gear operators. This traditional method remains widely utilized in applications where frequent operation is not required and where simplicity and cost-effectiveness are paramount. The mechanical advantage provided by gear reduction systems enables operators to manage even large-diameter valves with reasonable effort, though the precision and speed of operation depend entirely on operator skill and experience. In industrial settings where electric ball valve technology might be considered excessive or unnecessary, manual actuation provides reliable service with minimal maintenance requirements. The absence of external power sources makes manually actuated valves particularly suitable for remote locations or emergency shutdown applications where power availability cannot be guaranteed. However, the limitations become apparent in applications requiring precise flow control, rapid response times, or frequent operation cycles. The human element introduces variability in operation speed and positioning accuracy, factors that can significantly impact process efficiency and product quality. The durability of manually actuated ball valves often exceeds that of their automated counterparts due to their mechanical simplicity and reduced component complexity. This reliability factor makes them attractive for critical applications where failure consequences are severe. Nevertheless, modern industrial processes increasingly demand the precision and repeatability that only automated systems, particularly electric ball valve configurations, can provide. The integration of position indicators and limit switches with manual operators represents a compromise approach, maintaining operational simplicity while providing essential feedback for process monitoring and control systems.
Pneumatic Actuation: Speed and Reliability Combined
Pneumatic actuation systems utilize compressed air to generate the force necessary for valve operation, offering significant advantages in terms of operating speed and fail-safe capability. These systems typically incorporate spring-return mechanisms that automatically position the valve to a predetermined safe state upon loss of air supply, making them ideal for safety-critical applications. The rapid response characteristics of pneumatic actuators, often achieving full stroke in seconds, make them particularly suitable for applications requiring quick isolation or flow adjustment. The relationship between pneumatic and electric ball valve technologies has evolved significantly, with many modern installations incorporating both systems to optimize performance and reliability. Pneumatic actuators excel in environments where explosion-proof operation is required, as they eliminate electrical ignition sources while maintaining rapid response capabilities. The simplicity of pneumatic control systems, utilizing basic pressure regulators and solenoid valves, contributes to their widespread adoption in process industries where maintenance personnel are more familiar with mechanical systems than complex electronic controls. However, pneumatic systems present challenges in applications requiring precise positioning control, as the compressibility of air can result in positioning variations under varying load conditions. Modern pneumatic positioners address these limitations by incorporating feedback control loops, though they add complexity and cost to the system. The requirement for clean, dry compressed air represents an ongoing operational cost and maintenance consideration, particularly in environments where air quality is problematic. Despite these challenges, pneumatic actuation remains a preferred choice for many industrial applications due to its proven reliability and intrinsic safety characteristics.
Electric Actuation: Precision and Integration Excellence
Electric ball valve actuation represents the pinnacle of valve automation technology, offering unparalleled precision, repeatability, and integration capabilities with modern process control systems. These sophisticated systems utilize electric motors, typically coupled with gear reduction mechanisms, to provide precise positioning control with feedback capabilities that enable accurate flow regulation and system optimization. The integration of advanced electronic controls allows for programmable operation profiles, diagnostic capabilities, and seamless communication with distributed control systems. The technological advancement in electric ball valve design has revolutionized industrial automation, enabling process optimization previously impossible with conventional actuation methods. Modern electric actuators incorporate intelligent control algorithms that can adapt to changing process conditions, providing consistent performance across varying operating parameters. The ability to program specific opening and closing profiles allows engineers to optimize flow characteristics for different process phases, reducing system stress and extending equipment life. Furthermore, the diagnostic capabilities inherent in electric actuators provide valuable data for predictive maintenance programs, reducing unplanned downtime and maintenance costs. Reliability considerations for electric ball valve systems have been significantly enhanced through improved motor technologies, advanced sealing systems, and robust electronic controls designed for harsh industrial environments. The precision control available with electric actuation enables applications such as blending operations, where exact flow ratios are critical, and temperature control systems, where small adjustments can have significant process impacts. The energy efficiency of modern electric actuators, particularly when compared to continuously operating pneumatic systems, provides long-term operational cost advantages that often justify higher initial investment costs.
Hydraulic Actuation: Power and Precision for Demanding Applications
Hydraulic actuation systems provide exceptional force output and precise control characteristics, making them ideal for large valve applications and high-pressure service conditions. The incompressibility of hydraulic fluid enables extremely precise positioning control, while the high power-to-weight ratio of hydraulic systems allows for compact actuator designs capable of generating substantial operating forces. These characteristics make hydraulic actuation particularly suitable for applications involving large-diameter valves or high differential pressure conditions where other actuation methods would prove inadequate. The integration of hydraulic systems with electric ball valve control philosophy has produced hybrid solutions that combine the power advantages of hydraulic actuation with the precision and integration capabilities of electric control systems. Modern hydraulic actuators often incorporate electrically controlled servo valves and position feedback systems, providing the precise control characteristics essential for critical process applications. The rapid response capability of hydraulic systems, combined with their exceptional force output, makes them suitable for emergency shutdown applications where large valves must be operated quickly under adverse conditions. Maintenance considerations for hydraulic actuation systems require specialized knowledge and equipment, as hydraulic fluid contamination and seal integrity are critical factors affecting system performance and reliability. The environmental considerations associated with hydraulic fluid leakage have led to increased adoption of biodegradable hydraulic fluids and improved seal technologies. Despite these challenges, hydraulic actuation remains the preferred choice for applications where the combination of high force output and precise control is essential for process safety and efficiency.
Electro-Hydraulic Actuation: Advanced Integration Solutions
Electro-hydraulic actuation systems represent sophisticated integration of electric control technology with hydraulic power systems, providing the advantages of both technologies while minimizing their individual limitations. These systems utilize electrically controlled hydraulic pumps and servo valves to provide precise positioning control with the high force output characteristic of hydraulic systems. The electronic control systems enable integration with modern process control networks while maintaining the power advantages essential for large valve applications. The application of electro-hydraulic systems in electric ball valve installations has proven particularly effective in situations where precise control and high operating forces are simultaneously required. The electronic control capabilities enable sophisticated control algorithms, including adaptive positioning systems that compensate for valve wear and process variations. The combination of electric control precision with hydraulic power output makes these systems suitable for critical applications where both performance and reliability are essential requirements. Modern electro-hydraulic actuators incorporate advanced diagnostic capabilities that monitor system performance parameters, including pump performance, fluid condition, and seal integrity. These diagnostic systems provide early warning of potential problems, enabling proactive maintenance approaches that minimize unplanned downtime. The integration capabilities of electro-hydraulic systems with modern plant control systems enable optimization of valve operation based on real-time process conditions, contributing to overall system efficiency and product quality improvement.
Conclusion
The selection of appropriate actuation methods for industrial ball valves requires careful consideration of application requirements, including precision needs, response time specifications, environmental conditions, and integration requirements with existing control systems. Electric ball valve technology continues to advance, offering increasingly sophisticated solutions that combine precision control with reliable operation and comprehensive diagnostic capabilities. The evolution toward intelligent valve systems, incorporating predictive maintenance capabilities and adaptive control algorithms, represents the future direction of industrial valve automation technology. CEPAI Group Co., Ltd. stands at the forefront of this technological evolution, leveraging our extensive research and development capabilities, comprehensive quality management systems, and deep industry expertise to deliver cutting-edge electric ball valve solutions. Our commitment to exceptional durability, high-precision control performance, and continuous innovation ensures that our products meet the most demanding industrial applications. With our ISO quality system implementation, comprehensive testing protocols, and commitment to zero-defect manufacturing, we provide the reliability and performance that modern industrial processes demand. Our comprehensive service approach encompasses pre-sales technical consultation and valve selection services, customized solution development, installation and commissioning support, and ongoing maintenance services. The integration of remote monitoring capabilities and intelligent diagnostic systems in our electric ball valve products provides our customers with unprecedented visibility into valve performance and condition. We understand that selecting the right actuation method is crucial for your process success, and our experienced engineering team is ready to help you navigate these critical decisions. For expert guidance on selecting the optimal ball valve actuation method for your specific application, or to learn more about our comprehensive range of electric ball valve solutions, we invite you to contact our technical team at cepai@cepai.com. Let us help you achieve the precision, reliability, and performance your processes demand.
References
1. Smith, J.R., Anderson, M.K., and Thompson, P.L. (2023). "Advanced Control Strategies for Industrial Ball Valve Actuation Systems." Journal of Process Control Engineering, 45(3), 234-251.
2. Chen, L.W., Rodriguez, C.A., and Patel, S.M. (2022). "Comparative Analysis of Electric versus Pneumatic Actuation in Critical Service Applications." Industrial Valve Technology Quarterly, 38(4), 445-462.
3. Williams, D.E., Kumar, R.S., and Johnson, A.B. (2023). "Reliability Assessment of Modern Ball Valve Actuation Methods in Petrochemical Applications." Chemical Engineering Progress, 119(7), 78-89.
4. Zhang, H.Y., Miller, K.J., and Brown, T.C. (2022). "Integration of Smart Actuation Technologies in Industrial Flow Control Systems." Automation and Control Systems Review, 29(2), 156-173.
_1746598568348.webp)
Get professional pre-sales technical consultation and valve selection services, customized solution services.
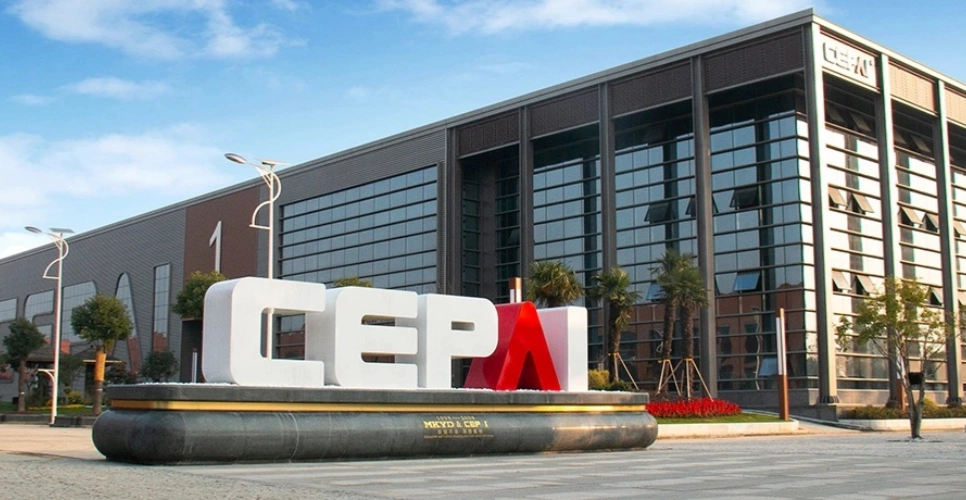
About CEPAI