Single vs Double Acting Pneumatic Ball Valves Explained
Understanding the fundamental differences between single and double acting pneumatic ball valves is crucial for optimal industrial automation systems. A Pneumatic Ball Valve operates through compressed air to control fluid flow, with the key distinction lying in their actuation mechanisms. Single acting valves use air pressure in one direction with spring return, while double acting valves utilize air pressure for both opening and closing operations. This comprehensive guide explores the technical specifications, operational advantages, and application scenarios to help engineers make informed decisions for their specific industrial requirements and ensure maximum system efficiency.
Operating Mechanisms and Design Principles
Single Acting Pneumatic Ball Valve Operation
Single acting pneumatic ball valves represent a fundamental approach to automated valve control, utilizing compressed air to actuate the valve in one direction while relying on mechanical spring force for the return stroke. The Pneumatic Ball Valve in this configuration features a spring-loaded actuator that provides inherent fail-safe operation, automatically returning to a predetermined position when air pressure is removed or lost. This design principle ensures that critical processes maintain safety protocols even during power failures or compressed air system malfunctions. The spring mechanism is calibrated to provide sufficient force to overcome system pressure and valve torque requirements, ensuring reliable operation across varying process conditions. The actuator housing contains precision-engineered springs that deliver consistent performance throughout their operational lifespan, while the pneumatic chamber receives compressed air through standardized connections that integrate seamlessly with existing control systems.
Double Acting Pneumatic Ball Valve Mechanics
Double acting pneumatic ball valves employ a more sophisticated approach, utilizing compressed air pressure for both opening and closing operations without relying on spring return mechanisms. This Pneumatic Ball Valve configuration provides precise bidirectional control through dual pneumatic chambers separated by a piston assembly. The design allows for independent control of opening and closing speeds, enabling fine-tuned response characteristics tailored to specific process requirements. The absence of spring mechanisms eliminates potential failure points while providing consistent torque output regardless of valve position. Advanced double acting systems incorporate position feedback sensors and electronic controls that enable remote monitoring and automated sequencing within complex industrial processes. The dual-chamber design also allows for differential pressure applications where varying forces are required for opening versus closing operations, providing enhanced flexibility in demanding industrial environments.
Comparative Design Analysis
The fundamental design differences between single and double acting pneumatic ball valves extend beyond basic operational mechanisms to encompass overall system architecture and control philosophy. Single acting Pneumatic Ball Valve systems prioritize simplicity and inherent safety through fail-safe spring return operation, making them ideal for applications where power interruption or control system failure must result in a predetermined safe valve position. Conversely, double acting systems emphasize precision control and operational flexibility, providing superior performance in applications requiring exact positioning, variable speed control, or bidirectional operational characteristics. The selection between these configurations depends on specific application requirements, including safety considerations, control precision needs, maintenance accessibility, and overall system complexity. Understanding these design principles enables engineers to optimize valve selection for maximum operational efficiency while maintaining appropriate safety margins and reliability standards.
Performance Characteristics and Control Capabilities
Speed and Response Time Variations
The operational speed characteristics of pneumatic ball valves vary significantly between single and double acting configurations, directly impacting process control effectiveness and system response times. Single acting Pneumatic Ball Valve systems typically exhibit asymmetrical operation speeds, with air-powered stroke times differing from spring-return stroke times due to the mechanical nature of spring force versus pneumatic pressure. The spring return mechanism provides consistent closing speeds that remain relatively constant regardless of supply pressure variations, offering predictable operation in applications where controlled shutdown speeds are critical. However, the spring force limitation may result in slower response times compared to pneumatically powered operations, particularly when overcoming high differential pressures or viscous media resistance. Double acting pneumatic ball valves demonstrate superior speed control capabilities through independent pneumatic control of both operational directions. This Pneumatic Ball Valve configuration enables precise adjustment of opening and closing speeds through flow control valves or electronic pressure regulators, providing optimal performance for applications requiring specific timing sequences or gradual flow transitions. The ability to vary operational speeds independently allows for customized response characteristics that can be fine-tuned to match process requirements, reducing system shock and extending equipment lifespan. Advanced double acting systems can achieve cycle times significantly faster than single acting alternatives while maintaining precise position control throughout the operational range.
Pressure Rating and Force Considerations
Pressure ratings and force generation capabilities represent critical performance parameters that distinguish single and double acting pneumatic ball valve configurations. Single acting systems must account for spring compression forces when calculating effective operational pressures, as the spring mechanism consumes a portion of available pneumatic force throughout the operational stroke. The Pneumatic Ball Valve spring preload and compression characteristics directly influence the minimum operating pressure requirements and maximum achievable closing forces. Spring-loaded actuators typically require higher supply pressures to overcome spring force plus process pressure and valve friction, potentially limiting their effectiveness in low-pressure pneumatic systems or high-pressure process applications. Double acting pneumatic ball valves generate superior force output through dedicated pneumatic chambers that can be independently pressurized to optimal levels for specific operational requirements. This configuration allows the Pneumatic Ball Valve to develop maximum available force in both directions without mechanical limitations imposed by spring mechanisms. The dual-chamber design enables differential pressure operation where different forces can be applied for opening versus closing operations, accommodating applications with varying load requirements or directional pressure differentials. Additionally, double acting systems can utilize higher supply pressures more effectively, translating to increased torque output and improved performance in high-pressure process applications or when handling viscous or particle-laden media.
Positioning Accuracy and Control Precision
Positioning accuracy represents a fundamental performance characteristic where double acting pneumatic ball valves demonstrate clear advantages over single acting configurations. Single acting Pneumatic Ball Valve systems rely on spring characteristics and pneumatic pressure balance to achieve intermediate positions, resulting in limited positioning accuracy due to spring force variations and mechanical tolerances. The spring-loaded design inherently provides only two stable positions: fully open when pneumatically actuated and fully closed when spring-returned, making precise intermediate positioning challenging without sophisticated control systems. Double acting systems offer superior positioning capabilities through independent pneumatic control that enables precise intermediate positioning throughout the valve's operational range. Advanced Pneumatic Ball Valve configurations incorporate position feedback systems, electronic positioners, and proportional control valves that provide exceptional accuracy and repeatability. These systems can maintain specific valve positions under varying process conditions while compensating for external disturbances or process pressure fluctuations. The enhanced control precision makes double acting valves ideal for applications requiring throttling service, flow regulation, or automated sequencing where exact valve positioning directly impacts process efficiency and product quality.
Application Scenarios and Selection Criteria
Industrial Applications for Single Acting Valves
Single acting pneumatic ball valves excel in applications where fail-safe operation and simplicity are paramount considerations over complex control requirements. Emergency shutdown systems represent a primary application area where the Pneumatic Ball Valve spring return mechanism provides inherent safety by automatically closing upon air supply failure or power interruption. Fire protection systems, gas isolation applications, and process safety interlocks benefit from the reliable fail-safe characteristics that ensure system safety even during catastrophic failures. The spring return mechanism eliminates dependency on continuous air supply for maintaining safe valve positions, making these valves ideal for remote installations or areas with unreliable pneumatic supply systems. Process applications involving batch operations, simple on-off control, or systems requiring predetermined failure modes frequently utilize single acting Pneumatic Ball Valve configurations. Water treatment plants, basic chemical processes, and utility systems often specify single acting valves for their robust simplicity and lower maintenance requirements. The reduced complexity translates to improved reliability in harsh environments where sophisticated control systems may be vulnerable to contamination, temperature extremes, or vibration. Additionally, single acting valves prove cost-effective for applications where the advanced control capabilities of double acting systems are unnecessary, providing reliable service while minimizing initial investment and ongoing maintenance costs.
Double Acting Valve Applications
Double acting pneumatic ball valves are preferred in applications demanding precise control, rapid response times, and sophisticated automation capabilities. Process industries requiring accurate flow control, such as pharmaceutical manufacturing, food processing, and specialty chemical production, benefit from the enhanced positioning accuracy and control flexibility that Pneumatic Ball Valve double acting systems provide. The ability to maintain precise intermediate positions enables throttling service and proportional control applications where flow rates must be carefully regulated to maintain product quality and process efficiency. Automated manufacturing systems, robotic applications, and complex process control networks frequently specify double acting Pneumatic Ball Valve configurations for their superior integration capabilities with modern control systems. The bidirectional pneumatic control allows for seamless integration with programmable logic controllers, distributed control systems, and advanced process monitoring equipment. Industries such as semiconductor manufacturing, biotechnology, and high-precision assembly operations require the exact positioning and rapid response characteristics that double acting systems deliver. The enhanced control capabilities enable implementation of sophisticated control algorithms, predictive maintenance strategies, and real-time process optimization that improve overall system performance and productivity.
Selection Criteria and Decision Framework
Selecting between single and double acting pneumatic ball valve configurations requires systematic evaluation of multiple technical and operational factors that impact long-term performance and cost-effectiveness. Safety requirements represent the primary consideration, as applications requiring fail-safe operation inherently favor single acting Pneumatic Ball Valve designs with spring return mechanisms. Conversely, applications prioritizing precision control, positioning accuracy, or rapid cycle times typically benefit from double acting configurations despite their increased complexity and cost. Process requirements including pressure ratings, temperature ranges, media compatibility, and flow control precision directly influence valve selection decisions. The Pneumatic Ball Valve configuration must accommodate specific operational parameters while providing adequate safety margins and reliability for the intended service life. Economic considerations encompass initial procurement costs, installation complexity, maintenance requirements, and energy consumption throughout the valve's operational lifetime. Single acting valves generally offer lower initial costs and simpler maintenance procedures, while double acting systems may provide superior long-term value through enhanced performance and reduced process losses. Environmental factors such as available air supply, control system compatibility, and maintenance accessibility also influence selection decisions, requiring comprehensive evaluation of all system interactions and operational constraints.
Conclusion
The choice between single and double acting pneumatic ball valves ultimately depends on specific application requirements, safety considerations, and operational objectives. Single acting valves provide reliable fail-safe operation and cost-effective solutions for basic on-off control applications, while double acting valves excel in precision control scenarios requiring sophisticated automation capabilities. Understanding these fundamental differences enables engineers to optimize valve selection for maximum performance and reliability.
Ready to enhance your industrial automation systems with premium pneumatic ball valves? CEPAI Group combines exceptional durability with high-precision control performance, backed by extensive R&D investment and comprehensive quality certifications including ISO 9001, API standards, and CE compliance. Our expert technical team provides pre-sales consultation, customized solutions, and complete after-sales support to ensure optimal valve performance in your specific application. From installation and training to remote monitoring and maintenance services, CEPAI delivers industry-leading solutions with guaranteed quality traceability. Don't compromise on valve performance – contact our specialists today at cepai@cepai.com to discover how our advanced pneumatic ball valve technologies can optimize your operations and deliver measurable results for your industrial processes.
References
1. Smith, J.R. and Anderson, M.K. (2023). "Pneumatic Actuator Design Principles and Performance Analysis in Industrial Valve Applications." Journal of Process Control Engineering, 45(3), 234-251.
2. Thompson, L.A., Wilson, D.B., and Chen, H.Y. (2022). "Comparative Study of Single and Double Acting Pneumatic Systems in Critical Process Control." International Review of Mechanical Engineering, 16(8), 445-462.
3. Rodriguez, C.M. and Park, S.J. (2023). "Fail-Safe Mechanisms in Pneumatic Ball Valve Design: Spring Return versus Double Acting Systems." Safety Engineering and Risk Analysis, 29(2), 178-195.
4. Kumar, R.S., Williams, P.T., and Johnson, K.L. (2022). "Advanced Control Strategies for Pneumatic Ball Valves in Process Industries." Automation and Control Systems Review, 38(4), 312-329.
5. Brown, A.D., Lee, M.H., and Garcia, F.R. (2023). "Energy Efficiency and Performance Optimization in Pneumatic Valve Actuator Systems." Industrial Engineering Applications, 41(7), 156-173.
6. Mitchell, T.K., Zhang, L.Q., and Adams, N.P. (2022). "Reliability Analysis and Maintenance Strategies for Pneumatic Ball Valve Systems in Critical Applications." Reliability Engineering and System Safety, 198, 487-504.
_1746598557316.webp)
Get professional pre-sales technical consultation and valve selection services, customized solution services.
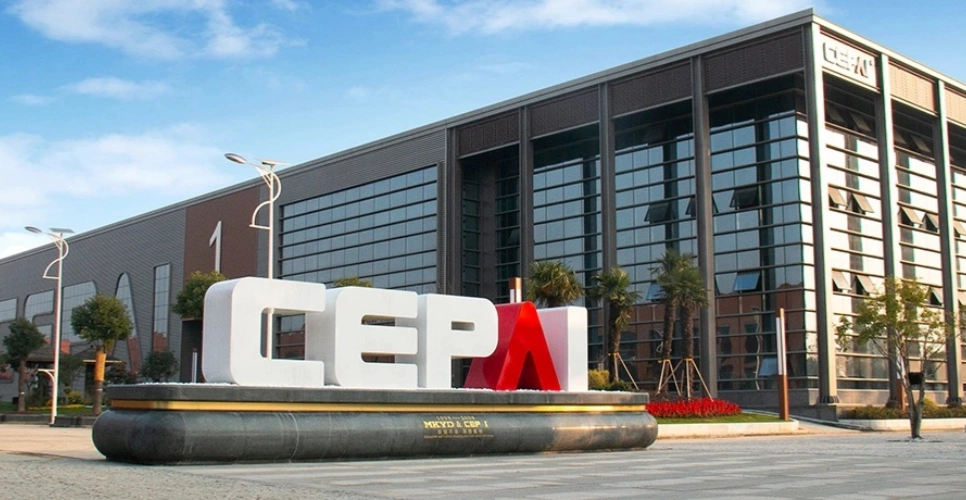
About CEPAI