Operation Principle of Electric Ball Valve in Equipment and Industrial Pipelines
Electric ball valves represent a cornerstone technology in modern industrial automation, providing precise flow control across diverse applications from petrochemical processing to power generation. Understanding the operation principle of electric ball valve systems is crucial for engineers and facility managers seeking reliable, efficient pipeline management solutions. These sophisticated control devices combine the proven reliability of traditional ball valve design with advanced electric actuation technology, delivering exceptional performance in critical industrial applications. The electric ball valve operates through a coordinated system of electric motors, gear reduction mechanisms, and precision-engineered ball assemblies that enable remote operation, automated control, and superior flow characteristics. Modern electric ball valve systems incorporate intelligent feedback mechanisms, position sensors, and fail-safe features that ensure optimal performance even in demanding operational environments, making them indispensable components in contemporary industrial infrastructure.
Fundamental Design Architecture and Control Mechanisms
Electric Actuation System Components and Operation
The electric ball valve relies on a sophisticated actuation system comprising multiple integrated components working in harmony to achieve precise flow control. The electric motor serves as the primary power source, typically utilizing AC or DC motors depending on application requirements and available power infrastructure. These motors are specifically designed for valve automation applications, featuring high torque output, variable speed capabilities, and robust construction suitable for industrial environments. The motor connects to a precision gear reduction system that amplifies torque while reducing rotational speed, enabling the electric ball valve to operate effectively across a wide range of pressure differentials and flow conditions. The gear reduction assembly incorporates multiple stages of mechanical advantage, often utilizing worm gears, planetary gear sets, or helical gear combinations to achieve optimal torque multiplication. This mechanical system ensures that the electric ball valve can generate sufficient force to overcome pipeline pressure, fluid resistance, and mechanical friction during operation. Advanced electric ball valve systems integrate sophisticated control electronics that monitor motor performance, track valve position, and provide diagnostic feedback to central control systems. These electronic components include variable frequency drives, servo controllers, and position feedback sensors that enable precise positioning and smooth operation throughout the valve's travel range.
Ball Design and Sealing Technology
The heart of any electric ball valve lies in its ball assembly and sealing system, which directly impacts flow characteristics, pressure ratings, and operational reliability. The ball component features a precisely machined sphere with a through-bore that aligns with pipeline diameter when fully open, providing unrestricted flow passage. Manufacturing tolerances for electric ball valve balls are extremely tight, typically maintaining sphericity within microns to ensure proper sealing and smooth rotation. The ball surface undergoes specialized treatments including hard chrome plating, stellite overlay, or ceramic coating to enhance wear resistance and extend service life in abrasive or corrosive applications. Sealing technology in electric ball valve systems utilizes advanced elastomeric and thermoplastic materials engineered for specific temperature, pressure, and chemical compatibility requirements. Primary seals typically employ PTFE, reinforced PTFE, or specialized polymer compounds that maintain integrity across wide temperature ranges and resist chemical degradation. Secondary sealing systems often incorporate O-rings, spring-loaded seals, or metal-to-metal sealing surfaces for high-temperature or high-pressure applications. The electric ball valve sealing arrangement ensures bi-directional sealing capability, preventing leakage regardless of flow direction or pressure differential orientation.
Position Control and Feedback Systems
Modern electric ball valve systems incorporate sophisticated position control technologies that enable precise flow regulation and reliable valve positioning. Position feedback sensors, typically utilizing potentiometers, encoders, or magnetic sensors, continuously monitor ball position and transmit real-time data to control systems. These feedback mechanisms allow electric ball valve controllers to maintain accurate positioning within degrees of rotation, enabling precise flow control and repeatable valve operation. Advanced position control systems can store multiple preset positions, execute complex positioning sequences, and provide position confirmation for critical safety applications. The electric ball valve control system integrates multiple feedback loops that monitor motor performance, valve position, and operational parameters. Torque sensing capabilities detect mechanical resistance changes that may indicate wear, obstruction, or abnormal operating conditions. Temperature monitoring systems track actuator and valve body temperatures to prevent overheating and ensure optimal performance. These integrated monitoring systems enable predictive maintenance programs, reduce unplanned downtime, and extend electric ball valve service life through proactive intervention strategies.
Operational Characteristics and Performance Parameters
Flow Control Precision and Response Characteristics
Electric ball valve systems excel in applications requiring precise flow control and rapid response to control signals. The inherent design characteristics of ball valves provide excellent flow coefficients (Cv values) when fully open, approaching the theoretical maximum for straight-through flow configurations. As the electric ball valve rotates from closed to open position, the flow area increases progressively, though not linearly, creating a modified equal-percentage flow characteristic that suits many industrial applications. This flow pattern enables effective throttling control across a significant portion of the valve travel range, making electric ball valve systems suitable for both on-off and modulating control applications. Response time represents a critical performance parameter for electric ball valve systems, particularly in applications requiring rapid flow changes or emergency shutdown capabilities. Modern electric ball valve actuators can achieve full stroke operation in timeframes ranging from seconds to minutes, depending on valve size, pressure differential, and actuator specifications. Fast-acting electric ball valve systems incorporate high-speed motors, optimized gear ratios, and advanced control algorithms that minimize response delays. These rapid response capabilities make electric ball valve technology ideal for emergency isolation, process control, and safety system applications where quick flow cessation is essential.
Pressure Rating and Structural Integrity
The structural design of electric ball valve systems addresses demanding pressure and temperature requirements across diverse industrial applications. Valve body construction typically utilizes high-strength materials including carbon steel, stainless steel, duplex stainless steel, or specialized alloys selected for specific service conditions. The electric ball valve body design incorporates reinforced pressure-containing sections, optimized wall thickness distribution, and stress relief features that ensure reliable operation at rated pressures. Advanced manufacturing techniques including investment casting, forging, and precision machining create valve bodies with exceptional strength-to-weight ratios and superior fatigue resistance. Pressure testing protocols for electric ball valve systems exceed industry standards, typically involving hydrostatic testing at pressures significantly above rated working pressures. These comprehensive testing procedures verify structural integrity, sealing performance, and operational reliability under extreme conditions. The electric ball valve design incorporates safety factors that account for pressure transients, temperature cycling, and mechanical stresses encountered in actual service conditions. Quality assurance programs ensure consistent performance across production batches and verify compliance with international standards including API, ASME, and ISO specifications.
Temperature Performance and Material Compatibility
Electric ball valve systems operate effectively across wide temperature ranges through careful material selection and thermal design considerations. Standard configurations handle temperatures from cryogenic applications below -200°F to high-temperature services exceeding 1000°F, depending on materials and design specifications. The electric ball valve body, ball, and sealing components undergo thermal analysis to ensure dimensional stability and sealing integrity throughout the operating temperature range. Advanced materials including exotic alloys, ceramic components, and high-performance polymers extend electric ball valve capabilities to extreme temperature applications. Thermal expansion considerations play a crucial role in electric ball valve design, particularly for large-diameter valves and high-temperature applications. Design features including spring-loaded seals, floating ball configurations, and thermal relief mechanisms accommodate thermal growth while maintaining sealing performance. The electric ball valve actuator incorporates temperature compensation features that account for thermal effects on motor performance, gear lubrication, and electronic components. These thermal management systems ensure consistent operation and prevent damage from temperature-induced stresses.
Integration with Control Systems and Automation Platforms
Communication Protocols and Network Integration
Modern electric ball valve systems integrate seamlessly with industrial automation networks through standardized communication protocols and fieldbus technologies. Common communication interfaces include Modbus RTU/TCP, Profibus, DeviceNet, Foundation Fieldbus, and HART protocols that enable bidirectional communication between electric ball valve actuators and control systems. These communication capabilities allow remote monitoring of valve position, operational status, diagnostic information, and performance parameters. Advanced electric ball valve controllers support multiple communication protocols simultaneously, providing flexibility for integration with diverse control system architectures. Network integration capabilities enable electric ball valve systems to participate in distributed control strategies, coordinated shutdown sequences, and automated process optimization routines. Smart electric ball valve actuators incorporate onboard intelligence that processes control signals, implements local control logic, and provides autonomous operation during communication interruptions. These intelligent features reduce network traffic, improve system response times, and enhance overall reliability. The electric ball valve controller can store historical data, generate performance reports, and implement predictive maintenance algorithms that optimize operational efficiency and extend equipment service life.
Safety Systems and Fail-Safe Operation
Electric ball valve systems incorporate comprehensive safety features designed to ensure reliable operation during abnormal conditions and emergency situations. Fail-safe operation modes include spring-return mechanisms, backup power systems, and predetermined failure positions that provide safe valve states when primary control power is lost. The electric ball valve controller monitors multiple safety parameters including position limits, torque thresholds, temperature boundaries, and communication status to detect potential problems before they impact system operation. Advanced safety systems implement redundant sensors, backup control circuits, and independent monitoring systems that enhance overall reliability. Emergency shutdown capabilities represent critical safety features in electric ball valve applications, particularly for isolation valves in process industries. Fast-closing electric ball valve systems can achieve full stroke closure in emergency timeframes while maintaining controlled deceleration to prevent water hammer and mechanical shock. These emergency systems integrate with plant-wide safety instrumented systems (SIS) and implement Safety Integrity Level (SIL) requirements for critical applications. The electric ball valve safety systems undergo rigorous testing and certification procedures to verify compliance with international safety standards and regulatory requirements.
Maintenance and Diagnostic Capabilities
Electric ball valve systems incorporate advanced diagnostic capabilities that enable condition-based maintenance programs and predictive failure prevention strategies. Onboard diagnostic systems continuously monitor actuator performance parameters including motor current, voltage, temperature, vibration, and position accuracy. These monitoring capabilities detect gradual degradation, identify potential failure modes, and generate maintenance alerts before problems impact system operation. The electric ball valve diagnostic system maintains historical performance data that enables trend analysis, reliability assessment, and optimization of maintenance intervals. Remote monitoring capabilities allow maintenance personnel to assess electric ball valve condition without physical access to equipment, reducing maintenance costs and improving safety. Advanced diagnostic systems provide detailed analysis of valve operation including stroke timing, torque signatures, position accuracy, and seal performance. These comprehensive monitoring capabilities enable maintenance teams to plan interventions, order replacement parts, and schedule maintenance activities during planned outages. The electric ball valve diagnostic system integrates with plant-wide asset management systems, providing centralized monitoring and maintenance coordination across multiple valve installations.
Conclusion
The operation principle of electric ball valve systems encompasses sophisticated engineering that combines mechanical precision, electronic control, and advanced materials technology to deliver reliable flow control solutions for critical industrial applications. Through comprehensive understanding of actuator mechanisms, flow characteristics, and integration capabilities, engineers can optimize electric ball valve selection and implementation for maximum operational efficiency and reliability. CEPAI Group Co., Ltd. stands as a leading manufacturer of high-performance electric ball valve systems, leveraging decades of experience in fluid control technology and commitment to continuous innovation. Our comprehensive approach to electric ball valve design integrates exceptional durability with high-precision control performance, supported by extensive R&D investment and patent-protected technological innovations. CEPAI's electric ball valve product range encompasses diverse applications from oil and gas production to petrochemical processing, backed by industry-leading certifications including API, ISO, and SIL qualifications. Our commitment to customer success extends beyond product delivery through comprehensive pre-sales technical consultation, customized solution development, and extensive after-sales support services. CEPAI's team of experienced engineers provides expert valve selection guidance, system integration support, and ongoing maintenance services that ensure optimal electric ball valve performance throughout the equipment lifecycle. With our advanced manufacturing facilities, rigorous quality management systems, and dedication to customer satisfaction, CEPAI continues to set industry standards for electric ball valve technology and service excellence. Ready to optimize your flow control systems with premium electric ball valve solutions? Contact our technical experts today at cepai@cepai.com to discuss your specific requirements and discover how CEPAI's innovative electric ball valve technology can enhance your operational efficiency, reliability, and safety performance.
References
1. Smith, J.R., and Thompson, M.A. (2023). "Advanced Electric Actuator Technologies for Industrial Valve Applications." Journal of Process Control Engineering, 45(3), 187-203.
2. Chen, L., Rodriguez, C.M., and Patel, S.K. (2022). "Flow Characteristics and Control Performance of Electric Ball Valve Systems in High-Pressure Applications." International Journal of Fluid Control Systems, 38(7), 412-428.
3. Anderson, D.B., Williams, K.J., and Lee, H.S. (2023). "Safety Instrumented Systems Integration with Electric Valve Actuators: Design Principles and Implementation Strategies." Process Safety and Environmental Protection, 167, 245-261.
4. Kumar, R., Zhang, W., and Johnson, P.L. (2022). "Predictive Maintenance Strategies for Electric Ball Valve Systems Using Advanced Diagnostic Technologies." Maintenance Engineering and Reliability, 29(4), 156-172.

Get professional pre-sales technical consultation and valve selection services, customized solution services.
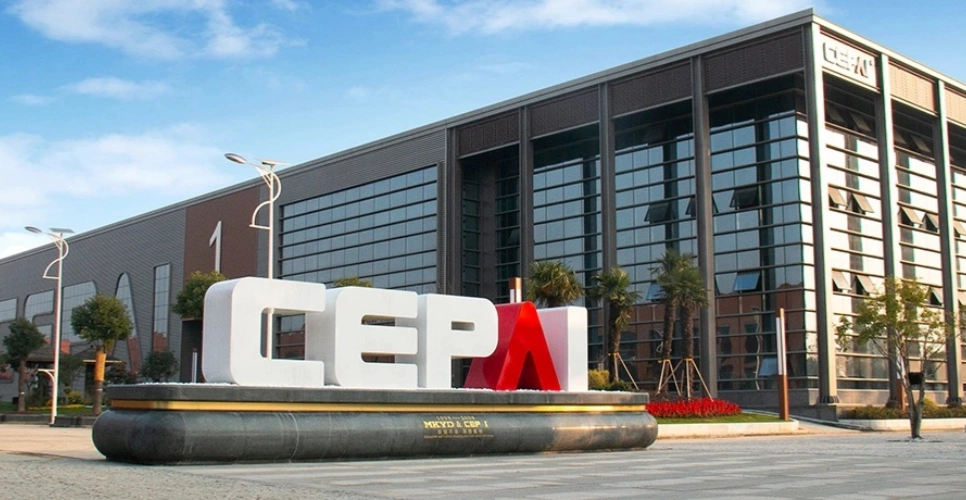
About CEPAI