Electric Ball Valve Buying Guide for Industrial Applications
Selecting the right electric ball valve for your industrial application is a critical decision that impacts operational efficiency, safety, and long-term cost-effectiveness. This comprehensive guide walks you through the essential considerations when purchasing electric ball valves, from understanding fundamental specifications to evaluating advanced features for specialized industrial environments. Whether you're managing oil and gas operations, chemical processing facilities, or power generation plants, this guide will equip you with the knowledge to make informed decisions when investing in electric ball valves that meet your specific requirements and industry standards.
Understanding Electric Ball Valve Fundamentals
Choosing the appropriate electric ball valve requires a thorough understanding of their core components, operational principles, and the various configurations available in today's market. This foundational knowledge will help you navigate the technical specifications and make informed decisions based on your specific industrial requirements.
Key Components and Construction Materials
Electric ball valves are sophisticated control devices comprising several critical components that work in harmony to deliver precise flow control. The main body is typically constructed from materials such as stainless steel, carbon steel, or specialized alloys depending on the application environment. The selection of body material directly impacts the valve's pressure rating, temperature tolerance, and resistance to corrosion. For instance, 316 stainless steel electric ball valves offer excellent resistance to chemical corrosion, making them ideal for aggressive media, while carbon steel variants provide superior strength for high-pressure applications. The valve ball—the core component that rotates to permit or block flow—must be manufactured with exceptional precision to ensure proper sealing and smooth operation. Modern manufacturing techniques employ computer-controlled machining centers to achieve the necessary spherical perfection and surface finish. The valve seats, typically made from PTFE, RPTFE, or specialized elastomers, create the critical sealing interface with the ball. These materials must be carefully selected based on the process media's chemical composition, temperature range, and pressure conditions. The electric actuator, which provides the rotational force to operate the valve, consists of its own subsystem including motor, gearing, position sensors, and control electronics. High-quality electric ball valves feature actuators with protection ratings suitable for their intended environment, from simple indoor installations (IP65) to hazardous outdoor locations requiring explosion-proof certifications (ATEX, IECEx).
Operating Principles and Control Mechanisms
The fundamental operating principle of an electric ball valve revolves around the precision rotation of a spherical ball with a bore through its center. This rotation is carefully controlled by the electric actuator, which converts electrical energy into rotational mechanical energy. When the bore aligns with the flow path, the valve permits full flow; when rotated 90 degrees, it completely blocks flow. This quarter-turn operation makes electric ball valves particularly efficient for quick opening and closing applications. Modern electric ball valves incorporate sophisticated control mechanisms that extend far beyond simple open/close functionality. Many feature modulating control capabilities, allowing for incremental positioning between 0% and 100% open. This precision is achieved through various feedback systems, including potentiometers, encoders, or Hall-effect sensors that continuously monitor the valve's position. The control interface may include analog signals (4-20mA, 0-10V), digital protocols (HART, Foundation Fieldbus, Profibus), or newer industrial IoT connectivity options. Advanced electric ball valves feature intelligent positioning systems that compensate for mechanical wear and environmental changes, maintaining precise control throughout the valve's service life. These systems continuously monitor torque requirements and position accuracy, adjusting parameters as needed to maintain optimal performance. Additionally, many electric ball valves now incorporate fail-safe mechanisms that move the valve to a predetermined safe position (open, closed, or current position) in case of power failure, using capacitors, battery backups, or mechanical spring-return systems.
Types and Configurations for Different Applications
Electric ball valves come in various configurations, each designed to address specific application requirements and installation constraints. The two-piece design represents the most common and economical configuration, featuring a body split into two sections joined by bolts, making maintenance relatively straightforward. More robust three-piece designs offer enhanced serviceability, allowing the center section containing the ball and seats to be removed without disturbing the connected piping—a significant advantage in critical process applications where downtime must be minimized. In terms of flow path design, full-bore (full-port) electric ball valves provide unobstructed flow when open, maintaining the same internal diameter as the connecting pipes. This design minimizes pressure drop and is essential for applications involving slurries, high-viscosity fluids, or those requiring pigging operations. Reduced-bore (standard-port) options offer a more compact and economical solution for applications where slight pressure drop is acceptable. For challenging control applications, characterized electric ball valves feature specially shaped balls or inserts that modify the flow profile as the valve opens, creating a more linear or equal-percentage flow characteristic. This makes them suitable for precise flow control applications that would traditionally require globe valves. Multi-port electric ball valves feature balls with multiple bores, allowing for complex flow diversion between three or more ports—ideal for applications requiring flow switching or diversion. Top-entry electric ball valves permit maintenance access from above without removing the valve from the line, a critical feature for applications where continuous process integrity must be maintained.
Selection Criteria for Industrial Electric Ball Valves
When selecting electric ball valves for industrial applications, several critical factors must be evaluated to ensure optimal performance, safety, and longevity. Understanding these selection criteria will help you make informed decisions that align with your specific industrial requirements and operational conditions.
Pressure and Temperature Ratings
Pressure and temperature ratings represent fundamental considerations when selecting electric ball valves for industrial applications. These ratings define the operational envelope within which the valve can safely and effectively function. Industry standards such as ANSI/ASME B16.34, API 6D, and EN 12516 establish standardized pressure classes (such as Class 150, 300, 600, 900, 1500, and 2500) that correspond to specific pressure-temperature relationships. It's essential to understand that a valve's pressure rating decreases as the operating temperature increases due to the changing material properties. For instance, a Class 600 electric ball valve rated for 1480 PSI at ambient temperature might only be suitable for 1040 PSI at 400°F. Comprehensive pressure-temperature (P/T) charts provided by manufacturers should be carefully consulted during the selection process. Beyond steady-state conditions, considerations must include pressure transients, thermal cycling, and potential vacuum conditions. High-performance electric ball valves designed for severe service applications incorporate reinforced body designs, special ball-to-seat loading mechanisms, and advanced sealing technologies to maintain integrity under extreme conditions. Temperature extremes present particular challenges for electric ball valve selection. At elevated temperatures, concerns include thermal expansion of components, potential stress relaxation in fasteners, and changes in material properties that can affect sealing performance. Specialized high-temperature electric ball valves may incorporate graphite-reinforced PTFE seats, metal-to-metal seating surfaces, or exotic alloy components to maintain functionality at temperatures exceeding 500°F. Conversely, cryogenic applications require special consideration for material brittleness, thermal contraction, and specialized seat designs to maintain sealing integrity at extremely low temperatures.
Media Compatibility and Corrosion Resistance
The compatibility between the electric ball valve's materials of construction and the process media represents a critical factor in ensuring long-term performance and safety. Improper material selection can lead to accelerated corrosion, component degradation, and ultimately valve failure—potentially resulting in expensive downtime, product loss, or safety incidents. Chemical compatibility must be evaluated not just for the primary valve body material but also for all wetted components including the ball, stem, seats, seals, and any internal components. Industry reference tools such as chemical resistance charts provide general guidance, but for critical applications or unique process fluids, more detailed analysis or laboratory testing may be necessary. For aggressive chemical applications, electric ball valves constructed from specialized alloys such as Hastelloy, Monel, Inconel, or titanium offer exceptional corrosion resistance. These materials, while more expensive initially, often provide superior total cost of ownership through extended service life and reduced maintenance requirements. Erosion resistance represents another important consideration, particularly in applications involving abrasive slurries, catalyst-laden fluids, or high-velocity gases. Specialized electric ball valves featuring hardened surfaces through processes like hard chrome plating, thermal spraying, or the application of tungsten carbide overlays can dramatically extend service life in erosive conditions. Environmental factors external to the process must also be considered, especially for electric ball valves installed in marine environments, chemical processing areas, or locations subject to atmospheric pollutants. The actuator housing and external valve components should incorporate appropriate protection including specialized coatings, sealed enclosures (meeting IP66/68 standards), and corrosion-resistant fasteners. Regular inspection protocols should be established to monitor for signs of corrosion, particularly at material transitions and seal boundaries where crevice corrosion can occur.
Electric Actuator Specifications
The electric actuator represents the active component of an electric ball valve assembly, providing the motive force and control intelligence necessary for reliable operation. Proper actuator specification requires careful consideration of torque requirements throughout the valve's operating range. The required torque varies significantly based on valve size, pressure differential, seating forces, and safety factors. Reputable manufacturers provide detailed torque calculation tools that account for these variables plus additional factors such as stem friction, bearing loads, and seal compression. Sizing should account for both breakaway torque (the initial force required to begin valve movement from a stationary position) and running torque (the force required to maintain movement once started). A safety factor of at least 25% is typically recommended to account for process variations, valve wear, and emergency conditions. Power supply considerations are equally important, with options including AC power (single-phase or three-phase at various voltages) or DC power (typically 24V for control systems integration). Power consumption during operation and holding positions should be evaluated, particularly for remote installations with limited power availability or battery backup systems. Control interface selection depends on the complexity of the application and integration with existing control systems. Options range from simple on/off control using discrete inputs to proportional control utilizing analog signals (4-20mA, 0-10V) to advanced digital communication protocols (MODBUS, PROFIBUS, FOUNDATION Fieldbus, HART) that provide additional diagnostic capabilities and parameter adjustment. Environmental protection must match the installation conditions, with appropriate ingress protection (IP) ratings for dust and moisture resistance. For hazardous area installations, explosion-proof or intrinsically safe actuators certified to relevant standards (ATEX, IECEx, FM, CSA) must be specified. Additional features to consider include manual override capabilities (handwheel, declutchable gearbox), position indicators, anti-condensation heaters for humid environments, and programmable functions such as speed control or intermediate positioning.
Advanced Features and Technological Innovations
The evolution of electric ball valves has accelerated in recent years, incorporating sophisticated technologies that enhance performance, reliability, and integration capabilities. Understanding these advanced features will help you select valves that not only meet current requirements but position your operation for future technological advancements.
Smart Diagnostics and Predictive Maintenance
Modern electric ball valves increasingly incorporate intelligent diagnostic capabilities that transform traditional reactive maintenance approaches into proactive, condition-based strategies. These smart systems continuously monitor critical operational parameters including torque profiles, cycle counts, total travel, temperature, and vibration signatures. Advanced algorithms analyze this data to detect subtle changes that might indicate developing issues such as increased friction, seat wear, or actuator performance degradation. These early warning indicators allow maintenance teams to address potential problems before they result in unplanned downtime or catastrophic failure. Leading electric ball valve manufacturers now embed microprocessors directly within their actuators, creating devices capable of sophisticated self-diagnosis. These systems can differentiate between normal operational variations and genuine fault conditions, reducing false alarms while providing actionable intelligence. The diagnostic data is typically accessible through multiple interfaces, from local displays showing simple status indicators to comprehensive dashboards available through asset management software. For critical applications, real-time monitoring enables immediate notification of abnormal conditions through integration with distributed control systems (DCS) or dedicated alarm networks. Predictive maintenance capabilities represent the next evolutionary step beyond basic diagnostics. By establishing baseline performance parameters during commissioning and tracking trends over time, these systems can predict remaining useful life and optimal maintenance timing with remarkable accuracy. For instance, by analyzing subtle changes in torque requirements during valve stroking, the system might identify developing stem packing compression issues months before they would be detected through conventional inspection methods. This predictive approach allows maintenance resources to be allocated more efficiently while minimizing spare parts inventory requirements. The most advanced electric ball valve systems now incorporate machine learning algorithms that continuously refine their predictive models based on operational experience, becoming increasingly accurate over time.
Integration with Industrial Control Systems
The seamless integration of electric ball valves with modern industrial control architectures represents a critical capability for optimizing process efficiency and operational flexibility. Today's advanced electric ball valves support multiple communication protocols, allowing them to interface directly with programmable logic controllers (PLCs), distributed control systems (DCS), and supervisory control and data acquisition (SCADA) networks. This direct digital integration eliminates the need for intermediate conversion devices, reducing potential points of failure while improving data integrity and response times. Standard industrial protocols supported by modern electric ball valves include HART (Highway Addressable Remote Transducer), which superimposes digital signals on conventional 4-20mA analog signals, enabling bidirectional communication without additional wiring. More comprehensive digital protocols such as FOUNDATION Fieldbus, PROFIBUS, and MODBUS provide extended capabilities including remote configuration, multi-variable transmission, and detailed diagnostic information. For facilities embracing Industrial Internet of Things (IIoT) architectures, advanced electric ball valves now support protocols like OPC UA (Open Platform Communications Unified Architecture) and MQTT (Message Queuing Telemetry Transport) that facilitate secure, vendor-neutral data exchange across diverse systems. Integration extends beyond basic control functions to include asset management systems that maintain comprehensive electronic records of each valve's specification, maintenance history, and performance data. These systems simplify regulatory compliance documentation while providing valuable insights for continuous improvement initiatives. The incorporation of standardized electronic device description language (EDDL) or field device tool/device type manager (FDT/DTM) technologies ensures that electric ball valves can be seamlessly recognized and configured by compatible host systems regardless of manufacturer. This interoperability reduces commissioning time and simplifies system expansions or upgrades. Advanced integration capabilities also enable sophisticated control strategies such as model predictive control (MPC), which can leverage the precise positioning capabilities of electric ball valves to optimize complex process parameters across multiple variables simultaneously.
Energy Efficiency and Environmental Considerations
Environmental responsibility and energy efficiency have become increasingly important factors in industrial valve selection, reflecting both regulatory requirements and corporate sustainability commitments. Modern electric ball valves incorporate numerous design features specifically targeted at reducing environmental impact throughout their lifecycle. Energy consumption during operation represents an important consideration, particularly for installations with numerous valves or remote locations with limited power availability. Advanced motor and gearing designs have significantly reduced the power requirements of electric actuators. Variable frequency drives precisely match power input to actual torque requirements, while high-efficiency gear trains minimize mechanical losses. Some electric ball valve actuators now incorporate energy recovery systems that capture potential energy during closing operations and store it for use during subsequent opening cycles, further reducing net energy consumption. Fugitive emissions represent a critical environmental concern, particularly in applications involving volatile organic compounds, greenhouse gases, or toxic substances. High-performance electric ball valves designed to meet stringent standards such as ISO 15848 and API 641 incorporate specialized stem sealing systems, including multiple packing layers, live-loading mechanisms that maintain consistent compression despite thermal cycling, and advanced monitoring capabilities to detect potential leakage before it becomes significant. These low-emission designs not only reduce environmental impact but often result in substantial cost savings by minimizing product loss and avoiding regulatory penalties. The manufacturing processes and materials used in electric ball valve production also merit environmental consideration. Leading manufacturers have implemented sustainable practices including reduced energy consumption during manufacturing, responsible material sourcing, and designs optimized for eventual recycling. Documentation of these practices through environmental product declarations (EPDs) allows customers to make informed decisions aligned with their sustainability objectives. Lifecycle assessment (LCA) methodologies increasingly factor into procurement decisions, considering not just purchase price but total environmental impact from raw material extraction through eventual decommissioning. Advanced electric ball valves designed with modular components and easily replaceable wear parts contribute to circular economy principles by extending service life and reducing waste.
Conclusion
Selecting the right electric ball valve for your industrial application requires careful consideration of pressure-temperature ratings, media compatibility, actuator specifications, and technological features. As we've explored, modern electric ball valves offer unprecedented levels of control, reliability, and intelligent functionality that can significantly enhance operational efficiency. CEPAI Group, with our exceptional durability, high-precision control performance, and substantial R&D investments, stands ready to support your valve selection needs.
Ready to optimize your fluid control systems with industry-leading electric ball valves? Contact our team of valve experts for personalized technical consultation, customized solutions tailored to your specific requirements, and comprehensive after-sales support. Whether you need pre-sales technical guidance or ongoing maintenance assistance, CEPAI's commitment to quality and innovation ensures your success. Get in touch today at cepai@cepai.com and discover how our advanced electric ball valve technology can transform your industrial operations.
References
1. American Petroleum Institute. (2023). API Standard 6D: Specification for Pipeline and Piping Valves. Washington, DC: API Publishing Services.
2. Johnson, R. L., & Smith, A. B. (2024). Advanced Control Valve Technologies for Modern Industrial Applications. Journal of Process Engineering, 42(3), 218-234.
3. International Society of Automation. (2023). ISA-75.05.01: Control Valve Terminology. Research Triangle Park, NC: ISA Publishing.
4. Martinez, C., & Thompson, K. (2024). Smart Valve Technology: Integrating IoT Solutions in Process Industries. Industrial Automation Quarterly, 18(2), 156-172.
5. Chen, Y., & Williams, P. (2023). Materials Selection for Severe Service Electric Valves in Chemical Processing. Materials & Design, 215, 110-128.
6. Roberts, E. F., & Garcia, J. L. (2024). Energy Efficiency in Industrial Valve Systems: A Comprehensive Review. Energy Efficiency in Industrial Processes, 11(4), 302-319.
_1746598563385.webp)
Get professional pre-sales technical consultation and valve selection services, customized solution services.
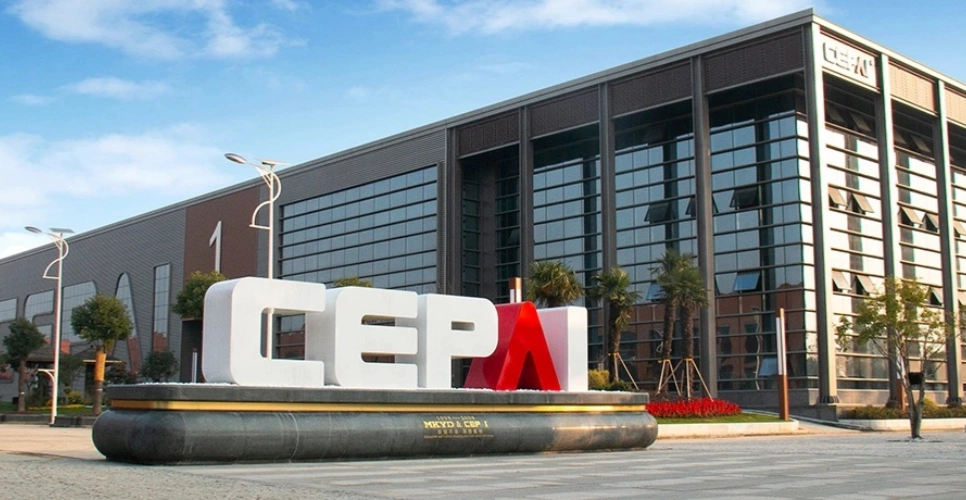
About CEPAI