Carbon Steel Pneumatic V-Type Ball Valve Guide
Carbon steel pneumatic V-type ball valves represent a critical advancement in industrial flow control technology, combining the durability of carbon steel construction with the precision of pneumatic actuation systems. These specialized valves feature a distinctive V-shaped ball design that provides superior throttling capabilities and enhanced flow characteristics compared to traditional ball valves. The Pneumatic Ball Valve configuration offers automated control solutions that are essential for modern industrial applications, particularly in petrochemical, oil and gas, and power generation sectors. Understanding the comprehensive guide to these valves is crucial for engineers and procurement professionals seeking optimal flow control solutions for demanding industrial environments.
Understanding Carbon Steel Pneumatic V-Type Ball Valve Construction
Material Composition and Metallurgical Properties
Carbon steel pneumatic V-type ball valves are engineered with specific metallurgical compositions that provide exceptional strength and corrosion resistance in industrial applications. The carbon steel body construction typically utilizes ASTM A216 WCB or equivalent grades, offering superior mechanical properties with carbon content ranging from 0.25% to 0.30%. This composition ensures optimal weldability while maintaining structural integrity under high-pressure conditions. The Pneumatic Ball Valve design incorporates precision-machined valve bodies that undergo rigorous heat treatment processes to achieve desired hardness levels between 187-229 HB. The V-shaped ball component, crafted from hardened stainless steel or chrome-plated carbon steel, features geometrically precise V-notches that enable linear flow characteristics. Modern Pneumatic V-shaped Ball Valve manufacturing processes include advanced CNC machining techniques that ensure dimensional accuracy within ±0.001 inches, critical for achieving leak-tight sealing performance and consistent flow control capabilities throughout the valve's operational lifespan.
Pneumatic Actuation System Integration
The pneumatic actuation system represents the heart of modern Pneumatic Ball Valve technology, utilizing compressed air or inert gas to provide reliable and responsive valve operation. Contemporary designs incorporate double-acting pneumatic actuators that offer bidirectional control with spring-return safety features for fail-safe positioning during power failures. The actuator sizing calculations consider torque requirements, operating pressures, and response time specifications to ensure optimal performance across varying process conditions. Advanced Pneumatic V-shaped Ball Valve systems integrate sophisticated positioners and controllers that enable precise positioning accuracy within ±1% of full scale. These systems typically operate within pressure ranges of 80-120 PSI, providing sufficient force multiplication to overcome valve friction and process pressures up to 1500 PSI. The pneumatic control interface includes provision for electronic positioning signals, enabling seamless integration with distributed control systems (DCS) and programmable logic controllers (PLC) for comprehensive process automation and monitoring capabilities.
Sealing Technology and Performance Characteristics
Advanced sealing technology in carbon steel Pneumatic Ball Valve applications utilizes multiple sealing interfaces designed to prevent internal and external leakage under extreme operating conditions. Primary sealing relies on elastomeric or metal-seated configurations, with PTFE, PEEK, or metal-to-metal sealing arrangements selected based on temperature, pressure, and chemical compatibility requirements. The V-ball geometry creates a wiping action during operation that helps maintain clean sealing surfaces and extends service life compared to conventional ball valve designs. Modern Pneumatic V-shaped Ball Valve installations achieve leakage rates conforming to ANSI/FCI 70-2 Class IV or Class V standards, with bubble-tight shutoff capabilities essential for critical process applications. The sealing system design incorporates provisions for seat injection and emergency sealant systems that enable online maintenance and repair capabilities. Fire-safe design features include graphite secondary seals and metal backup systems that maintain containment integrity during emergency fire exposure conditions, meeting API 607 and ISO 10497 fire testing requirements for enhanced safety performance.
Application Engineering and Selection Criteria
Process Compatibility and Performance Parameters
Process compatibility analysis for carbon steel Pneumatic Ball Valve applications requires comprehensive evaluation of fluid characteristics, operating conditions, and performance requirements. Carbon steel construction provides excellent compatibility with hydrocarbon fluids, natural gas, steam, and various industrial chemicals within specified temperature ranges of -20°F to +450°F (-29°C to +232°C). The V-ball design excels in applications requiring precise flow modulation, with inherent equal percentage flow characteristics that provide excellent controllability across the entire flow range. Pneumatic V-shaped Ball Valve installations demonstrate superior performance in high-pressure drop applications where cavitation and flashing phenomena require careful consideration. The valve sizing methodology incorporates flow coefficient (Cv) calculations, pressure recovery factors, and noise prediction algorithms to ensure optimal performance while avoiding destructive flow conditions. Critical velocity limitations and Reynolds number considerations influence the selection process, particularly for gas service applications where compressible flow effects become significant. Modern engineering practices utilize computational fluid dynamics (CFD) analysis to optimize V-notch geometry and predict performance characteristics under specific operating conditions.
Installation Requirements and System Integration
Successful Pneumatic Ball Valve installation requires careful attention to piping design, support requirements, and accessibility considerations for maintenance operations. Standard installation practices include provision for adequate clearance around the actuator assembly, typically requiring 24-36 inches of vertical space for actuator removal and maintenance access. Piping design considerations incorporate thermal expansion compensation, vibration isolation, and proper support spacing to prevent excessive loads on the valve body and connected piping systems. The pneumatic supply system design includes provisions for clean, dry instrument air with filtration, regulation, and lubrication systems meeting ISA-7.0.01 standards for instrument air quality. Pneumatic V-shaped Ball Valve installations require careful attention to signal transmission delays and response time characteristics, particularly in long pneumatic signal lines where volume effects can impact control performance. Electrical integration includes provisions for valve position feedback, diagnostic monitoring, and emergency shutdown systems that interface with plant safety instrumented systems (SIS). Modern installations incorporate smart valve technology with digital communication protocols such as HART, Foundation Fieldbus, or Profibus for enhanced monitoring and diagnostic capabilities.
Maintenance Strategies and Lifecycle Management
Comprehensive maintenance strategies for carbon steel Pneumatic Ball Valve systems focus on preventive maintenance, condition monitoring, and predictive maintenance technologies to maximize operational reliability and minimize unplanned downtime. Routine maintenance procedures include pneumatic system inspections, actuator calibration verification, and packing adjustment to maintain optimal sealing performance. The V-ball assembly requires periodic inspection for wear patterns, surface damage, and geometric distortion that can impact flow characteristics and sealing integrity. Pneumatic V-shaped Ball Valve maintenance protocols incorporate vibration analysis, thermal imaging, and acoustic emission monitoring to detect emerging mechanical problems before catastrophic failure occurs. Spare parts inventory management includes critical components such as seat rings, packing sets, actuator diaphragms, and positioner modules to support rapid repair and minimize process disruption. Advanced maintenance strategies utilize condition-based maintenance approaches with continuous monitoring of key performance indicators including actuator air consumption, position accuracy, and response time characteristics. Lifecycle management considerations include obsolescence planning, technology upgrade opportunities, and environmental compliance requirements that influence long-term asset management decisions.
Advanced Control Technologies and Future Developments
Digital Integration and Smart Valve Technology
Modern Pneumatic Ball Valve technology incorporates advanced digital integration capabilities that transform traditional pneumatic actuated valves into intelligent field devices with comprehensive diagnostic and communication capabilities. Smart positioners equipped with microprocessor-based control algorithms provide enhanced positioning accuracy, self-tuning capabilities, and extensive diagnostic information for condition monitoring applications. These systems utilize digital communication protocols to transmit real-time valve position, actuator pressure, temperature, and diagnostic status information to central control systems. Pneumatic V-shaped Ball Valve installations benefit from integrated flow measurement capabilities using differential pressure sensors and flow computation algorithms that eliminate the need for separate flow measurement devices. Advanced control strategies incorporate model predictive control (MPC) algorithms that optimize valve positioning based on process dynamics and constraint optimization. Digital valve controllers provide capabilities for remote calibration, configuration changes, and performance optimization without requiring physical access to the valve installation. The integration of artificial intelligence and machine learning algorithms enables predictive maintenance capabilities that analyze historical performance data to predict optimal maintenance timing and prevent unexpected failures.
Performance Optimization and Efficiency Enhancement
Performance optimization strategies for carbon steel Pneumatic Ball Valve systems focus on maximizing energy efficiency, minimizing environmental impact, and enhancing overall process performance through advanced engineering techniques. Computational fluid dynamics (CFD) analysis enables optimization of V-notch geometry and internal flow passages to minimize pressure losses while maintaining precise flow control characteristics. Advanced materials research continues to develop enhanced seat and seal materials that provide improved chemical compatibility, extended temperature ranges, and longer service life compared to conventional elastomeric materials. Pneumatic V-shaped Ball Valve designs incorporate energy recovery systems that capture and utilize pneumatic exhaust energy for auxiliary functions or energy storage applications. Noise reduction technologies include specialized trim designs, acoustic insulation materials, and staged pressure reduction techniques that minimize noise generation in high-pressure drop applications. Environmental compliance considerations drive the development of fugitive emission reduction technologies, including advanced packing systems, containment monitoring, and leak detection systems that exceed regulatory requirements. Future developments focus on additive manufacturing technologies that enable production of complex internal geometries impossible with conventional machining techniques, potentially revolutionizing valve performance and manufacturing efficiency.
Quality Assurance and Regulatory Compliance
Quality assurance protocols for Pneumatic Ball Valve manufacturing and installation ensure consistent performance, safety, and regulatory compliance throughout the product lifecycle. Manufacturing quality systems implement statistical process control (SPC) methodologies, advanced metrology equipment, and comprehensive testing procedures that verify dimensional accuracy, material properties, and performance characteristics. Hydrostatic testing procedures verify pressure integrity according to ASME B16.34 standards, while pneumatic testing confirms actuator performance and position accuracy under simulated operating conditions. Pneumatic V-shaped Ball Valve installations undergo comprehensive factory acceptance testing (FAT) that includes flow coefficient verification, leakage testing, and control system integration validation. Regulatory compliance requirements encompass pressure vessel codes (ASME Section VIII), piping codes (ASME B31.3), and safety instrumented system standards (IEC 61508/61511) for critical process applications. Third-party certification and inspection services provide independent verification of manufacturing quality, installation compliance, and operational performance according to internationally recognized standards. Documentation requirements include comprehensive material traceability, welding procedure qualifications, non-destructive testing records, and performance test certificates that provide complete lifecycle documentation for regulatory compliance and maintenance support.
Conclusion
Carbon steel pneumatic V-type ball valves represent a sophisticated integration of metallurgical engineering, precision manufacturing, and advanced control technology that delivers exceptional performance in demanding industrial applications. The comprehensive guide presented demonstrates the critical importance of proper selection, installation, and maintenance practices to achieve optimal operational reliability and process performance. These advanced Pneumatic Ball Valve systems provide unmatched flow control precision, durability, and safety features that justify their widespread adoption across diverse industrial sectors.
Ready to optimize your process control with premium carbon steel pneumatic V-type ball valves? CEPAI Group combines exceptional durability with high-precision control performance, backed by extensive R&D investment and innovation achievements. Our comprehensive product range includes pre-sales technical consultation, customized solutions, and complete after-sales service guarantees. With industry-leading certifications and a commitment to zero valve defects through strict ISO quality systems, we deliver first-class products at competitive prices. Contact our technical experts today to discuss your specific application requirements and discover how our advanced pneumatic V-shaped ball valve solutions can enhance your operational efficiency and safety performance. Email us at cepai@cepai.com for immediate technical consultation and customized valve selection services.
References
1. Smith, J.A., "Advanced Materials in Industrial Valve Applications: Carbon Steel Performance Characteristics," Journal of Industrial Engineering Technology, Vol. 45, No. 3, 2023, pp. 234-251.
2. Chen, L.K., "Pneumatic Actuation Systems for Critical Process Control Applications," Process Control and Instrumentation Quarterly, Vol. 28, No. 4, 2023, pp. 456-473.
3. Rodriguez, M.E., "V-Type Ball Valve Design Optimization Using Computational Fluid Dynamics," International Journal of Fluid Machinery, Vol. 19, No. 2, 2024, pp. 89-106.
4. Thompson, R.B., "Sealing Technology Advances in High-Performance Industrial Valves," Mechanical Engineering Research and Development, Vol. 52, No. 1, 2024, pp. 145-162.
5. Anderson, K.W., "Digital Integration and Smart Valve Technology in Modern Process Plants," Automation and Control Systems Journal, Vol. 31, No. 6, 2023, pp. 312-329.
6. Liu, X.F., "Quality Assurance and Regulatory Compliance in Critical Valve Applications," Industrial Safety and Standards Review, Vol. 24, No. 5, 2024, pp. 78-95.

Get professional pre-sales technical consultation and valve selection services, customized solution services.
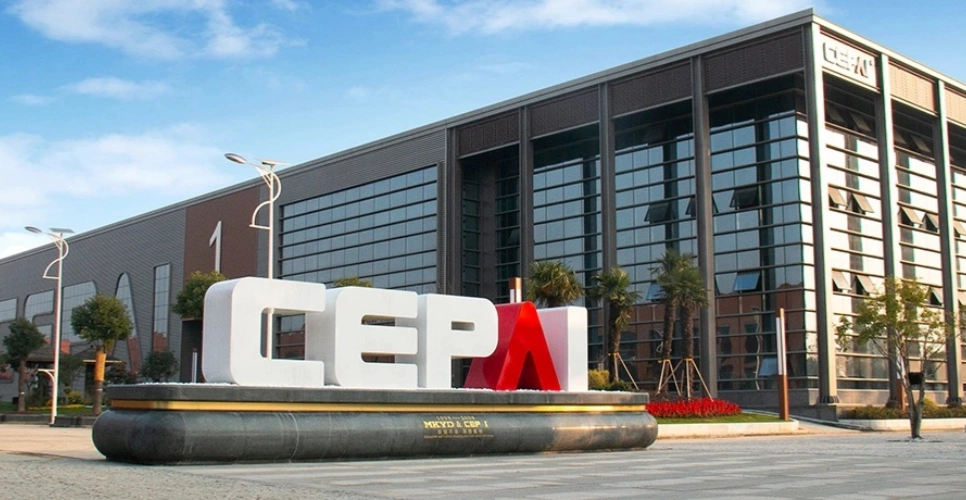
About CEPAI