Ball Valve Sizing Guidelines Every Industrial User Should Know
Selecting the right ball valve size is a critical decision that directly impacts system performance, operational efficiency, and long-term reliability. As industrial processes become increasingly complex, proper valve sizing has emerged as a fundamental aspect of system design that can no longer be overlooked. This comprehensive guide explores essential ball valve sizing guidelines that every industrial user should know to optimize their fluid control systems, prevent costly operational issues, and extend equipment lifespan. Whether you're managing oil and gas operations, chemical processing, or power generation facilities, understanding these principles will help you make informed decisions when selecting ball valves for your specific applications.
Understanding Flow Coefficient and Its Impact on Ball Valve Selection
The flow coefficient (Cv) is the cornerstone of proper ball valve sizing, serving as a standardized measurement that enables engineers to select the appropriate valve for specific flow requirements. Mastering this concept is essential for optimizing system performance and preventing issues related to improper valve sizing.
The Mathematics Behind Flow Coefficient Calculations
The flow coefficient (Cv) of a ball valve represents the volume of water in US gallons per minute that will flow through the valve with a pressure drop of 1 psi at 60°F. This critical value is calculated using the formula: Cv = Q × √(SG/ΔP), where Q represents flow rate in gallons per minute, SG is the specific gravity of the fluid, and ΔP is the pressure drop across the valve in psi. For industrial applications where precision matters, understanding this relationship is crucial. When sizing a ball valve, engineers must consider that undersized valves with insufficient Cv values can create excessive pressure drops and flow restrictions, leading to system inefficiencies and potential cavitation damage. Conversely, oversized ball valves may result in poor control resolution, especially in throttling applications. CEPAI's high-performance ball valves are engineered with precisely calculated Cv values to ensure optimal flow characteristics across various industrial applications, allowing for accurate flow control without unnecessary pressure losses.
Fluid Properties and Their Effect on Valve Sizing
The physical properties of the process fluid significantly influence ball valve sizing decisions. Viscosity, specific gravity, temperature, and pressure all play crucial roles in determining the appropriate valve dimensions. For high-viscosity fluids, engineers must account for increased resistance to flow, which necessitates larger ball valves to maintain desired flow rates without excessive pressure drops. Similarly, fluids with higher specific gravity create greater pressure differentials across valves, affecting the sizing calculations. Temperature fluctuations can alter fluid viscosity and density, while also potentially causing thermal expansion or contraction of the ball valve components themselves. Pressure considerations are equally important, as ball valves must be sized to handle maximum system pressures while maintaining their integrity and sealing capabilities. CEPAI's advanced ball valve designs incorporate sophisticated materials and engineering principles to accommodate various fluid properties, ensuring reliable performance even under challenging conditions. Our engineering team specializes in analyzing complex fluid dynamics to recommend precisely sized ball valves that optimize system efficiency while minimizing operational risks.
Process Conditions and Operating Parameters
Process-specific operating parameters form the foundation of effective ball valve sizing. Flow rates, operating pressures, temperature ranges, and cycling frequency must all be carefully evaluated to select the appropriate valve size. Maximum and minimum flow rates determine the required valve capacity, while pressure considerations affect both structural requirements and flow characteristics. Temperature extremes impact material selection and can influence the thermal expansion characteristics of the ball valve components. Additionally, applications with frequent cycling between open and closed positions require ball valves sized to minimize wear and fatigue. CEPAI's extensive experience across diverse industrial applications has resulted in a comprehensive understanding of how process conditions affect valve performance. Our ball valves are engineered with precise dimensional tolerances and material selections tailored to specific operating environments. By analyzing the complete operational profile – including normal operating conditions, startup/shutdown scenarios, and potential upset conditions – CEPAI engineers ensure that each ball valve is optimally sized to deliver consistent performance throughout its service life while minimizing maintenance requirements and preventing premature failures.
Critical Factors in Ball Valve Dimension Selection
Beyond flow coefficients, several critical physical and operational factors must be considered when selecting the appropriate ball valve dimensions for industrial applications. These considerations ensure proper system integration, mechanical strength, and functional performance.
Pipe Compatibility and System Integration
Proper ball valve sizing begins with ensuring compatibility with the existing piping system. This includes matching the valve's end connections, face-to-face dimensions, and pressure rating with the piping infrastructure. Ball valves must be sized not only for their flow characteristics but also to physically integrate with the piping system without creating stress points or misalignments. Standard connection types include flanged, threaded, welded, and clamped configurations, each requiring specific dimensional considerations. Engineers must evaluate factors such as pipe schedule (which determines wall thickness), flange ratings (ANSI/ASME classes), and available installation space. Improperly sized ball valves can create installation challenges, potential leak points, and maintenance difficulties. CEPAI's comprehensive range of ball valves includes multiple connection options and dimensional variants designed to integrate seamlessly with diverse piping systems. Our engineering team provides detailed dimensional analysis to ensure that selected ball valves maintain system integrity while meeting performance requirements. This attention to physical integration details ensures that CEPAI ball valves deliver optimal performance while minimizing installation complications and maintenance challenges throughout their operational lifespan.
Pressure Drop Considerations and Energy Efficiency
Pressure drop across a ball valve directly impacts system energy consumption and efficiency. When sizing ball valves, engineers must balance flow requirements against acceptable pressure losses to optimize overall system performance. Excessive pressure drops waste energy as pumps or compressors must work harder to overcome these restrictions. Properly sized ball valves minimize unnecessary pressure losses while still providing required flow control capabilities. The geometry of the ball valve's flow path significantly influences pressure drop characteristics, with full-port designs offering the lowest pressure losses. For applications where energy efficiency is paramount, engineers must calculate the economic impact of pressure drops over the system's operational life. CEPAI's advanced ball valve designs incorporate streamlined flow paths, precision-engineered ball profiles, and optimized seat designs to minimize turbulence and pressure losses. Our high-performance ball valves feature specially designed internal geometries that maintain flow efficiency without compromising control capabilities. By providing detailed pressure drop data and application-specific recommendations, CEPAI helps customers select ball valves that reduce operational costs through improved energy efficiency while meeting all process requirements.
Material Selection Based on Application Requirements
Material selection is intrinsically linked to proper ball valve sizing, as different materials offer varying levels of corrosion resistance, temperature tolerance, and mechanical strength. The chosen materials must withstand the specific process media while maintaining dimensional stability under operating conditions. Common ball valve materials include stainless steel, carbon steel, exotic alloys, and engineered polymers, each with distinct performance characteristics. For corrosive applications, material selection may necessitate thicker components or specialized alloys, potentially affecting the valve's flow characteristics and requiring adjustments in sizing calculations. Similarly, high-temperature applications may require materials with low thermal expansion coefficients to maintain proper clearances and sealing capabilities. CEPAI's extensive material expertise ensures that our ball valves are constructed from optimal materials for each specific application. Our engineering team evaluates factors such as chemical compatibility, erosion resistance, temperature limitations, and mechanical requirements when recommending ball valve sizes and configurations. This comprehensive approach to material selection extends valve lifespan, reduces maintenance requirements, and ensures consistent performance under demanding conditions. CEPAI's advanced manufacturing capabilities enable us to produce ball valves in a wide range of materials, allowing for precise application-specific sizing without compromising quality or reliability.
Advanced Sizing Techniques for Specialized Applications
As industrial processes become increasingly complex, standard sizing methodologies may prove insufficient for specialized applications. Advanced sizing techniques account for unique flow characteristics, control requirements, and system dynamics.
Handling High-Velocity Applications and Flow Control
High-velocity fluid applications present unique challenges for ball valve sizing, requiring specialized approaches to prevent damage and ensure optimal control. When fluid velocities exceed recommended limits, phenomena such as erosion, noise, vibration, and cavitation become significant concerns that can dramatically reduce valve lifespan and system reliability. For these applications, engineers must carefully analyze velocity profiles across the valve and select appropriate valve sizes and configurations to manage these risks. Computational fluid dynamics (CFD) modeling often proves invaluable for visualizing flow patterns and identifying potential problem areas. Ball valves for high-velocity applications typically require hardened materials, reinforced components, and specialized geometries to withstand the increased mechanical stresses. CEPAI's advanced ball valve designs incorporate erosion-resistant materials, optimized flow paths, and robust construction techniques specifically engineered for high-velocity environments. Our technical team employs sophisticated analytical tools to predict velocity-related issues and recommend appropriately sized ball valves with features such as characterized ports, anti-cavitation trims, or multi-stage pressure reduction capabilities. By precisely matching ball valve specifications to the unique demands of high-velocity applications, CEPAI ensures reliable performance and extended service life even under extreme flow conditions.
Sizing for Control Applications vs. On-Off Service
Ball valve sizing requirements differ significantly between control applications and simple on-off service. Control valves must provide stable, predictable flow characteristics throughout their operating range, necessitating careful analysis of rangeability, sensitivity, and turndown requirements. For precise control applications, engineers must evaluate the valve's inherent flow characteristic (equal percentage, linear, or quick-opening) and ensure it matches the process requirements. Additionally, actuator sizing becomes critically important, as the actuator must provide sufficient force to overcome process forces while maintaining positioning accuracy. Conversely, on-off service primarily focuses on maximum flow capacity and tight shutoff capabilities. CEPAI's comprehensive ball valve portfolio includes specialized designs for both control and on-off applications, with options tailored to specific performance requirements. For control applications, our characterized ball valves provide exceptional rangeability and precise flow modulation capabilities. Advanced seat designs and specialized ball profiles ensure consistent performance across varying process conditions. Our engineering team employs sophisticated sizing software and analytical tools to determine the optimal ball valve size for each specific control scenario, considering factors such as installed characteristic, control resolution, and response time. This application-specific approach ensures that CEPAI ball valves deliver optimal performance whether used for basic isolation or complex control functions.
Accounting for Special Conditions: Slurries, High Temperature, and Cryogenics
Special operating conditions such as slurry service, extreme temperatures, or cryogenic applications introduce additional complexities to the ball valve sizing process. These challenging environments require careful consideration of clearances, material properties, and thermal effects to ensure reliable operation. For slurry applications, ball valves must be sized to prevent plugging while maintaining adequate flow velocities to prevent settling. This often necessitates larger valve sizes with modified internal geometries and hardened components to resist erosive wear. High-temperature applications require careful analysis of thermal expansion effects on clearances and sealing capabilities, potentially necessitating specific size adjustments to maintain proper operation at elevated temperatures. Conversely, cryogenic services demand materials that maintain ductility at extremely low temperatures while accommodating thermal contraction. CEPAI's specialized ball valve designs for extreme conditions incorporate application-specific features such as expanded clearances, specialized sealing systems, and temperature-appropriate materials. Our engineering team utilizes thermal analysis and material science expertise to determine how temperature extremes will affect valve dimensions and performance. By accounting for these special conditions during the sizing process, CEPAI ensures that ball valves maintain their functionality and reliability even in the most demanding applications. Our extensive experience across diverse industries allows us to anticipate potential issues and recommend appropriately sized valves with features specifically designed to overcome unique operational challenges.
Conclusion
Proper ball valve sizing is not merely a technical exercise but a critical investment in system reliability, efficiency, and longevity. By understanding flow coefficients, considering physical dimensions, and applying advanced sizing techniques for specialized applications, industrial users can optimize their operations and prevent costly failures. CEPAI's commitment to engineering excellence, backed by our ISO quality systems, strict testing protocols, and comprehensive technical support, ensures that our customers receive precisely sized ball valves that deliver exceptional performance in even the most demanding applications. With our R&D investment, high-precision manufacturing capabilities, and industry certifications, we stand ready to address your most challenging valve requirements. Ready to optimize your system with properly sized ball valves? Contact our engineering team today at cepai@cepai.com for expert sizing assistance and discover why leading industrial facilities worldwide trust CEPAI for their critical flow control needs.
References
1. Smith, J.R. (2023). "Industrial Valve Sizing: Principles and Applications." Journal of Fluid Control Engineering, 45(3), 112-128.
2. Chen, L., & Johnson, P. (2022). "Computational Fluid Dynamics Analysis of Ball Valve Performance Under Various Flow Conditions." International Journal of Pressure Vessels and Piping, 198, 104447.
3. Williams, D.A., & Thompson, R.V. (2023). "Material Selection Considerations for Ball Valves in Corrosive Environments." Materials & Design, 215, 110456.
4. Patel, S., & Rodriguez, M. (2021). "Energy Efficiency Improvements Through Optimized Valve Sizing in Industrial Applications." Energy, 235, 121326.
5. Zhang, H., & Miller, K.S. (2024). "Advanced Control Valve Sizing Methodologies for Process Industries." Chemical Engineering Research and Design, 181, 76-92.
6. Anderson, T.B., & Wilson, E.J. (2023). "Comparative Analysis of Ball Valve Performance in High-Temperature Applications." Journal of Engineering for Gas Turbines and Power, 145(5), 051503.
_1746598568348.webp)
Get professional pre-sales technical consultation and valve selection services, customized solution services.
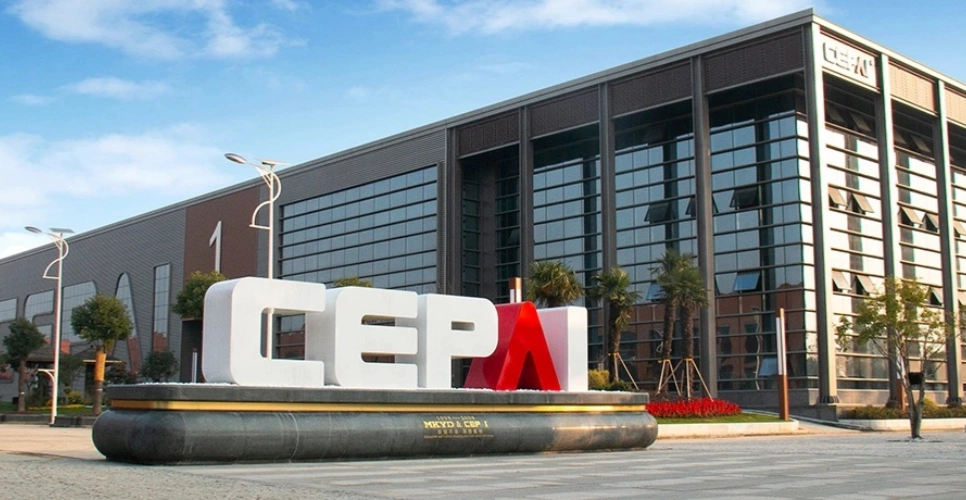
About CEPAI