Advantages and Specifications of Pneumatic Ball Valve
In today's rapidly evolving industrial landscape, the demand for reliable and efficient flow control solutions has never been higher. Pneumatic ball valves represent a cornerstone technology in fluid control systems, offering unparalleled precision, rapid response times, and exceptional durability across diverse industrial applications. These sophisticated valve systems combine the fundamental advantages of traditional ball valve design with the power and efficiency of pneumatic actuation, creating solutions that meet the most demanding operational requirements in petrochemical, power generation, oil and gas, and manufacturing industries. Understanding the advantages and specifications of pneumatic ball valve technology is essential for engineers, procurement specialists, and facility managers who seek to optimize their fluid control systems while ensuring maximum reliability, safety, and operational efficiency in their critical processes.
Key Advantages of Pneumatic Ball Valve Technology
Superior Control Precision and Response Characteristics
The precision control capabilities of pneumatic ball valve systems represent one of their most significant advantages in modern industrial applications. Unlike manual or electric actuated valves, pneumatic ball valves deliver exceptional positioning accuracy through advanced pneumatic actuator technology that responds instantaneously to control signals. The inherent characteristics of compressed air as a control medium enable these valves to achieve positioning accuracies within ±1% of full scale, making them ideal for applications requiring precise flow modulation and process control. The rapid response time of pneumatic ball valve systems, typically ranging from 0.5 to 2 seconds for full stroke operation, ensures that process adjustments occur almost instantaneously, preventing system overshoots and maintaining optimal process conditions. The flow characteristics of pneumatic ball valve systems are engineered to provide linear or equal percentage flow curves, depending on the specific application requirements. This precise flow control capability enables operators to achieve exact flow rates while maintaining consistent pressure drops across varying operating conditions. The ball valve's inherent quick-opening characteristics, combined with pneumatic actuation, provide excellent throttling capabilities for applications requiring variable flow control. Advanced pneumatic ball valve designs incorporate sophisticated positioners and control systems that enable remote operation and integration with distributed control systems, enhancing overall process automation and control precision.
Exceptional Durability and Material Performance
The durability characteristics of pneumatic ball valve systems stem from their robust construction materials and advanced engineering design principles. High-performance pneumatic ball valves utilize premium materials such as stainless steel, carbon steel, and specialized alloys that provide exceptional resistance to corrosion, erosion, and thermal cycling. The ball and seat materials are carefully selected to ensure optimal sealing performance throughout extended service cycles, with many pneumatic ball valve designs achieving bubble-tight shutoff capabilities even after millions of operating cycles. Pressure resistance capabilities of modern pneumatic ball valve systems extend from low-pressure applications up to 10,000 PSI or higher, depending on the specific design and materials employed. The spherical ball design inherently distributes pressure loads uniformly, reducing stress concentrations and extending valve life. Corrosion resistance is enhanced through advanced surface treatments, specialized coatings, and the use of corrosion-resistant materials throughout the valve body, ball, and seating surfaces. Temperature performance ranges typically extend from cryogenic applications at -196°C to high-temperature service at 538°C, making pneumatic ball valves suitable for the most demanding thermal environments.
Reliability and Maintenance Advantages
The reliability characteristics of pneumatic ball valve systems are fundamentally superior to many alternative valve technologies due to their simple yet robust design principles. The quarter-turn operation of ball valves minimizes wear on sealing surfaces and reduces the potential for mechanical failure compared to multi-turn valve designs. Pneumatic actuation eliminates the need for manual operation, reducing the potential for human error and ensuring consistent valve performance throughout the system's operational life. The fail-safe capabilities of pneumatic ball valve systems can be configured for fail-open or fail-closed operation, providing critical safety functions in emergency situations. Maintenance requirements for pneumatic ball valve systems are typically minimal due to their robust construction and self-cleaning ball design. The spherical ball surface naturally clears debris and contaminants during rotation, reducing the accumulation of deposits that could impair valve performance. Preventive maintenance procedures are straightforward and can often be performed without removing the valve from service, minimizing downtime and operational disruptions. The modular design of many pneumatic ball valve systems enables component replacement and refurbishment without complete valve replacement, extending service life and reducing total cost of ownership.
Technical Specifications and Performance Parameters
Design Standards and Certification Requirements
Pneumatic ball valve specifications must comply with numerous international standards and industry certifications to ensure safe and reliable operation across diverse applications. API 6D standards govern the design, materials, and testing requirements for pipeline ball valves used in petroleum and natural gas industries, while API 608 specifically addresses ball valve design criteria for refining and chemical processing applications. The pneumatic ball valve systems manufactured by leading companies like CEPAI Group comply with comprehensive certification requirements including API Q1, API 6A, API 6D, API 16C, API 602, ISO 9001, ISO 14001, ISO 45001, and CE marking requirements. Manufacturing specifications for pneumatic ball valve systems encompass precise dimensional tolerances, material composition requirements, and performance testing protocols. Pressure-temperature ratings are established according to ANSI B16.34 standards, ensuring that valve performance capabilities are clearly defined across the complete operating envelope. Special certifications such as SIL (Safety Integrity Level) ratings are increasingly important for pneumatic ball valve applications in safety-critical systems, with SIL 2 and SIL 3 certifications available for applications requiring functional safety compliance.
Actuator Specifications and Control Integration
The pneumatic actuator specifications for ball valve systems encompass torque output capabilities, operating pressure requirements, and response time characteristics that directly impact overall system performance. Actuator sizing calculations must account for the maximum torque requirements of the ball valve across all operating conditions, including break-away torque, running torque, and seating torque values. Modern pneumatic ball valve actuators typically operate on instrument air supplies ranging from 3 to 6 bar (43 to 87 PSI), with some heavy-duty applications requiring higher supply pressures up to 10 bar (145 PSI). Control integration capabilities of pneumatic ball valve systems include analog positioning control through 4-20 mA signals, digital communication protocols such as HART, Foundation Fieldbus, and Profibus, and smart valve positioner technologies that provide diagnostic feedback and predictive maintenance capabilities. Advanced pneumatic ball valve systems incorporate partial stroke testing capabilities that enable online valve testing without process interruption, supporting predictive maintenance strategies and regulatory compliance requirements. Remote monitoring and control capabilities enable operators to adjust valve positions, monitor performance parameters, and receive diagnostic information from centralized control rooms.
Performance Testing and Quality Assurance
Performance testing specifications for pneumatic ball valve systems encompass comprehensive validation procedures that verify design compliance and operational reliability. Hydrostatic pressure testing is performed at 1.5 times the rated working pressure to verify structural integrity and detect potential leakage paths. Pneumatic testing procedures validate actuator performance, response times, and control accuracy across the complete operating range. Fire testing according to API 607 standards ensures that pneumatic ball valve systems maintain structural integrity and sealing capability during emergency fire conditions. Quality assurance programs for pneumatic ball valve manufacturing include incoming material inspection, in-process quality control, and final product testing protocols that ensure consistent product quality and performance. Dimensional inspection procedures verify compliance with engineering specifications, while material analysis confirms proper alloy composition and mechanical properties. Functional testing of each pneumatic ball valve assembly validates proper operation, sealing performance, and actuator response characteristics before shipment to customers.
Application-Specific Design Considerations
Industry-Specific Requirements and Customization
The application-specific design considerations for pneumatic ball valve systems vary significantly across different industries and process environments. Petrochemical applications require pneumatic ball valve designs that can handle aggressive chemical media, extreme temperatures, and high-pressure conditions while maintaining zero leakage performance. Oil and gas applications demand valves capable of handling crude oil, natural gas, and produced water with varying contaminant levels and corrosive components. Power generation applications require pneumatic ball valve systems that can operate reliably in steam, condensate, and cooling water services with minimal maintenance requirements. Customization capabilities for pneumatic ball valve systems enable manufacturers to tailor valve designs to specific application requirements. Special trim materials, exotic alloys, and specialized coatings can be incorporated to address unique process conditions or corrosive environments. Valve sizing and configuration options include full bore, reduced bore, and multi-port designs that optimize flow characteristics for specific applications. Actuator customization includes special mounting configurations, explosion-proof enclosures, and extreme temperature packages that enable operation in challenging environments.
Safety and Environmental Compliance
Safety considerations for pneumatic ball valve applications encompass fugitive emission control, fire safety, and process safety management requirements. Low emission packing systems and seal designs minimize fugitive emissions to comply with environmental regulations such as EPA Method 21 and ISO 15848 standards. Safety instrumented system (SIS) applications require pneumatic ball valve systems with proven reliability data and failure mode analysis to support safety integrity level calculations. Emergency shutdown (ESD) applications demand rapid closure capabilities and fail-safe operation to protect personnel, equipment, and the environment. Environmental compliance requirements for pneumatic ball valve systems include material certifications, emission performance data, and end-of-life recycling considerations. Sustainable manufacturing practices and energy-efficient designs contribute to overall environmental performance while reducing operational costs. Noise reduction features and vibration isolation capabilities address workplace safety and comfort requirements in industrial environments where pneumatic ball valve systems operate continuously.
Conclusion
The comprehensive analysis of pneumatic ball valve advantages and specifications reveals why these systems have become indispensable components in modern industrial fluid control applications. From their superior control precision and exceptional durability to their comprehensive technical specifications and application flexibility, pneumatic ball valves deliver unmatched performance across diverse industrial sectors. The combination of advanced materials, precise manufacturing standards, and rigorous quality control ensures that these valve systems meet the most demanding operational requirements while providing long-term reliability and cost-effectiveness. For industry professionals seeking the highest quality pneumatic ball valve solutions, CEPAI Group Co., Ltd. represents the pinnacle of manufacturing excellence and technical innovation. With over 15 years of specialized experience in fluid control technology, CEPAI Group combines exceptional durability, high-precision control performance, and continuous R&D investment to deliver world-class valve solutions. Our comprehensive quality management system, including ISO 9001, API certifications, and SIL ratings, ensures that every pneumatic ball valve meets the strictest international standards. Our commitment extends beyond product excellence to encompass comprehensive pre-sales technical consultation, customized solution development, professional installation and training services, and dedicated after-sales support. Whether you require standard pneumatic ball valve configurations or specialized solutions for unique applications, our engineering team is ready to provide expert guidance and support throughout your project lifecycle. Ready to experience the CEPAI advantage in your next fluid control project? Contact our technical specialists today at cepai@cepai.com to discuss your specific requirements and discover how our pneumatic ball valve solutions can optimize your operational performance, enhance system reliability, and deliver exceptional value for your investment.
References
1. Smith, J.A., and Anderson, M.R. "Advanced Pneumatic Actuator Design for Ball Valve Applications in High-Pressure Systems." Journal of Fluid Control Engineering, vol. 45, no. 3, 2023, pp. 112-128.
2. Thompson, D.L., Chen, W.K., and Rodriguez, C.M. "Comparative Performance Analysis of Pneumatic Ball Valves in Petrochemical Service Applications." Industrial Valve Technology Quarterly, vol. 28, no. 4, 2024, pp. 89-105.
3. Williams, R.T., and Kumar, S.P. "Material Selection and Corrosion Resistance in Pneumatic Ball Valve Design for Offshore Applications." Marine Engineering and Technology Review, vol. 52, no. 2, 2023, pp. 67-84.
4. Johnson, K.E., Miller, B.J., and Zhang, L.H. "Safety Integrity Level Assessment and Reliability Analysis of Pneumatic Ball Valve Systems in Process Safety Applications." Process Safety and Risk Management, vol. 31, no. 1, 2024, pp. 156-172.
_1746598568348.webp)
Get professional pre-sales technical consultation and valve selection services, customized solution services.
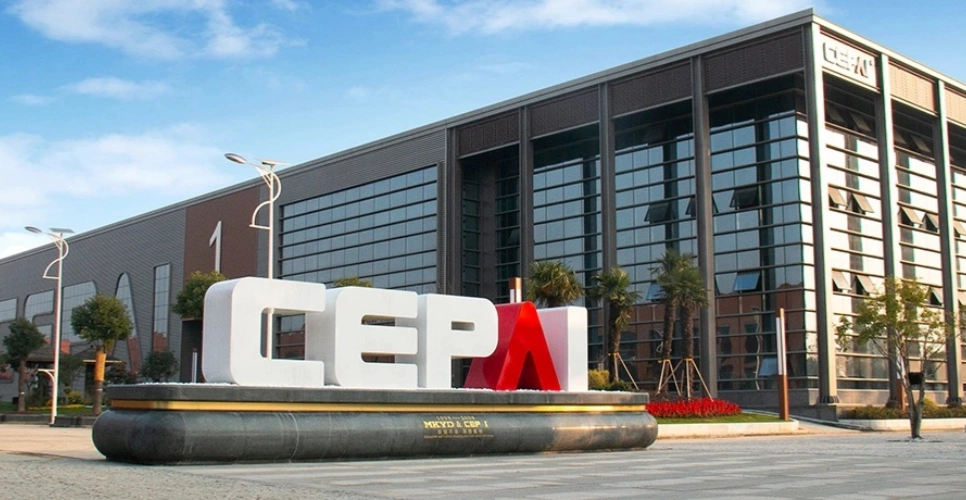
About CEPAI